The plastic recycling process today has losses and emissions, such as microplastics, inks and incorrectly sorted plastics. This prevents us from closing the plastic cycle. LEmPlaR focused on product losses and emissions in PP and PET recycling to increase the recycling yield of these plastics and reduce their environmental impact. Measurement techniques to assess losses, emissions, and contaminants, as well as the development of mitigation actions, were in scope.
In short:
- The project detected, quantified, and qualified the different losses and emissions in various parts of the sorting and washing cycle.
- Identified loss and emission hotspots in the recycling processes.
- Defined a mitigation strategy for different hotspots.
- Enabled recyclers to recycle plastics more efficiently by increasing the yield without impacting the environment.
How sorting plastics can impact the environment
Before we can recycle plastics, a complex sorting process takes place. First we collect the plastics, then we sort them, grind it into flakes, wash it, and finish with the sorting of flakes. These flakes can then be used for plastic recycling, for instance by mechanical recycling or with upcoming (thermo-)chemical recycling technologies.
Product losses decrease yield, while emissions, if improperly managed, can contaminate water sources, degrade air quality, and harm the environment. In the recycling process, examples of emissions and losses include incorrectly sorted plastics, microplastics, organic residue, inks, and adhesives. At the project’s start, there was a lack of quantitative data on these emissions and losses.
Overcoming product losses and increasing yield
The product losses, obviously, lead to a decreased yield but do also impact the environment. Some of the emissions (e.g. small particles) are a concern in water treatment, air quality and emission to the soil. With this project, we focused on the quantification and mitigation of these losses and emissions in plastic waste treatment for recycling with a special focus on PP and PET from municipal solid waste. The type of losses and emissions have been specified and quantified.
The project objectives were to:
- Being able to detect and quantify as well as qualify the different losses and emissions in different parts of the cycle
- Identify possible causes of plastic loss and unwanted emissions in the waste treatment process of municipal solid waste
- Define a mitigation strategy for different causes along complete R-ladder of circularity
- Enable recyclers to recycle plastics more efficiently by increasing the yield, without impacting the environment
Obtained results and insights
For this project, we mimicked the industrial recycling process of rigid PP packaging and PET trays using the reprocessing facilities at NTCP. We checked the layout against consulted high-quality industrial installations recyclers in the Netherlands to ensure that our installation closely resembled a real-size process. Using these setups, we performed trials on PP and PET with a large number of sampling points for different intermediate and output streams. This includes product, residue, and water samples. This is not yet common in the industry, where often only output streams are sampled.
We developed practical analytical tools to quantify losses, contaminants, and emissions to air, water, and solid waste using existing laboratory techniques. We distinguished air, water, and solid samples for this quantification:
Air:
We measured and analyzed airborne particles to identify their types and visualize their structure.
Water:
We tested the water for solids, pollutants, and overall cleanliness. We also checked for specific contaminants like nitrogen, PFAS substances, and microplastics.
Solids:
We assessed the moisture content, surface contamination, and composition of solid samples, and determined the size distribution of plastic flakes.
The major results of the trials are the mass balances over the whole process for each plastic. Below you will find several mass balances for typical reprocessing layouts. The focus of LEmPlaR was on PP and PET. However, the developed methods have also been applied to other plastics such as LDPE, LLDPE, and HDPE in different projects. This public report shows mass balances for the PP and PET in the respective recycling processes in Figure 1 and 2. The input of the process is always set to 100% of the target material, meaning that the input itself can still contain moisture, surface contamination, and other plastics.
Figure 1 – Mass balance for PP in the PP recycling process.
Note that contaminants are not shown in this mass balance.
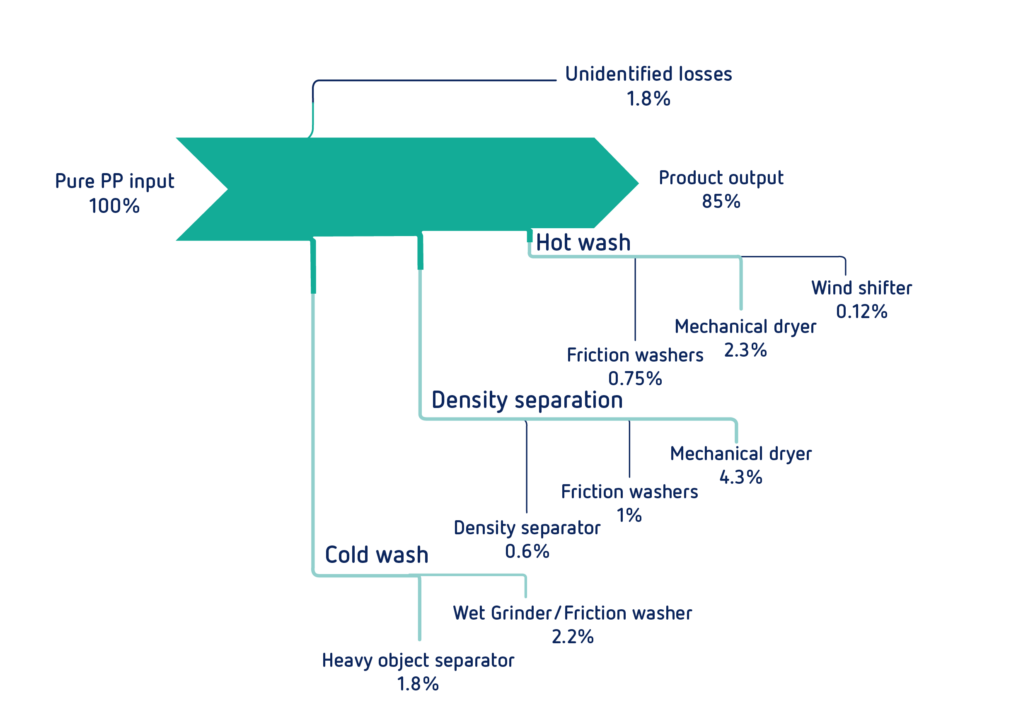
Figure 2 – Mass balance for PET in the PET recycling process.
Note that contaminants are not shown in this mass balance.
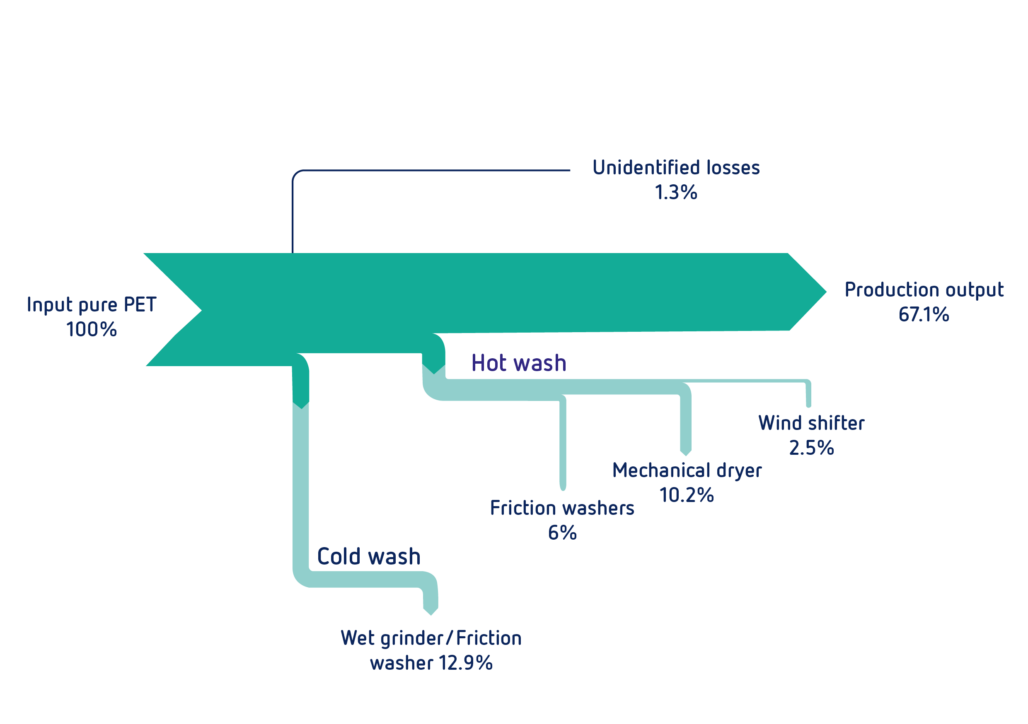
Cause for formation of losses and emissions discovered
In general, losses can be mitigated by choosing a sufficiently large screen in the wet granulator that is still small enough to enable efficient washing. This reduces the formation of microplastics below 2 mm that would be lost during the process. Additionally, we conclude that mechanical drying is a major cause of microplastic formation in mechanical recycling. This can be mitigated by reducing the centrifugal speed while monitoring the moisture content of the flakes.
Also interesting to read
You might also be interested in
Articles / Publications
Acknowledgement & partners
This project is co-funded with subsidy from the Topsector Energy by the Ministry of Economic Affairs and Climate Policy.
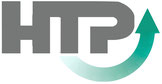
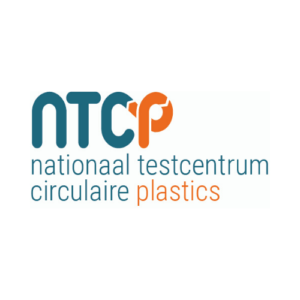
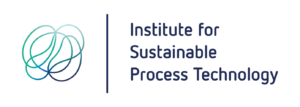

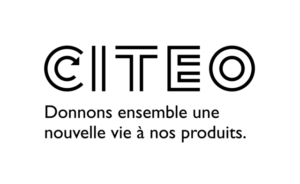
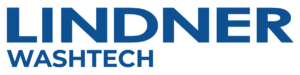
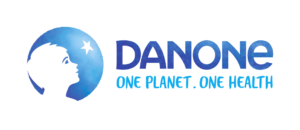
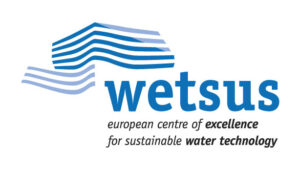
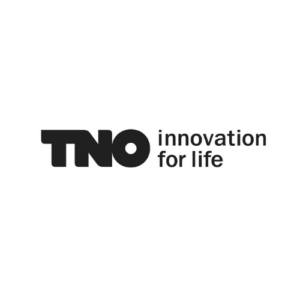
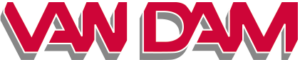