The Downstream ISolation of high-value Components (DISCO) project aimed to lower the CO2 footprint of downstream seperation technologies at FrieslandCampina, Corbion, Biota, Shell and Recell Group. By integrating innovative (membrane) technologies into existing or new production trains, efforts have been made to reduce material losses, energy consumption and waste flows.
In short:
- The CO2 footprint of downstream seperation technologies needs to be lowered
- DISCO evaluated current production trains and developed innovative production trains
- The objective was to lower the CO2 footprint of these innovative production trains by 50% in 2030
Energy- and material loss in separation technology
The CO2 footprint of the downstream separation technologies at FrieslandCampina, Corbion, Biota, Shell and Recell Group can be significantly lowered by using innovative technologies. Current production trains at these end-users produce a lot of material waste and use a lot of solvents (including water) which then must be purified or recovered. These purification and recovery steps in turn also use a lot of energy and materials.
Our ambition: increase energy efficiency
The objective of this 2.5-year project was to increase the energy efficiency of production and lower material use of the process trains at the end-users FrieslandCampina, Recell Group, Biota, Shell and Corbion. The DISCO project aspires to achieve a 50% reduction in CO₂ emissions from the implemented production trains by 2030. This translates to an estimated decrease of 0.27 megatons of CO₂ equivalents per year, accounting for approximately 2% of the total reductions pledged by the Dutch industry in the national climate agreement
Advanced separation technologies
The production trains of above mentioned end users are evaluated and innovative production trains were developed by using cutting edge, tailor-made technologies. The technologies used in these (new) production trains include:
- Nanofiltration (NF) Membranes: Utilized to selectively separate ions and small molecules, enhancing product purity and reducing energy consumption.
- Electrodialysis (ED): Employs electrical potential to drive ion migration through selective membranes, facilitating efficient desalination and deacidification processes.
- Ion Exchange Columns (IEX): Involve the exchange of ions between a solution and an ion-exchange resin, effectively removing undesirable ions and improving product quality.
- CO₂ Switch Technology: Developed by Greencovery, this method focuses on upcycling organic acids from industrial side streams, contributing to waste reduction and resource efficiency.
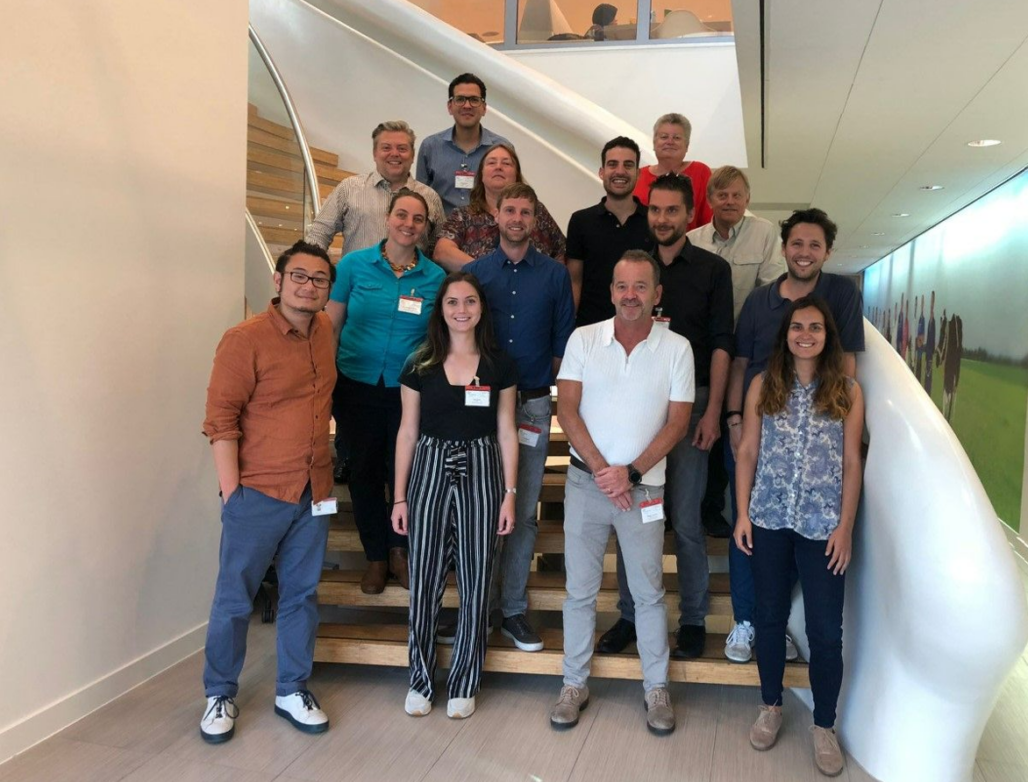
Activities & Results
The project combined fundamental research, technology development and techno-economic evaluations to arrive at scalable solutions. The four technologies (nanofiltration membranes, ion exchange, electrodialysis and CO2 switch) are evaluated and developed to better next generation technologies. The technologies were tested on pilot and bench scale. At the same time, business cases and sensitivity analyses were drawn up to map the economic feasibility of implementation.
Each partner in the DISCO project contributed specialized expertise to address distinct industrial challenges:
- FrieslandCampina explored the combination of nanofiltration and ion exchange to reduce ionic load on columns, enhancing production capacity while minimizing chemical use and wastewater generation.
- Recell Group focused on improving the quality of Recell Chem, a third-generation biobased product derived from waste streams, by optimizing downstream processing through membrane filtration and electrodialysis to expand market applications and increase product value.
- Biota Nutri investigated fermentation techniques to convert plant-based residual streams into volatile fatty acids (VFA) to improve calcium solubility and uptake in horticulture, with in-line extraction methods suggested for further optimization.
- Greencovery and Corbion collaborated to implement CO₂ switch technology for upcycling organic acids from industrial side streams, successfully achieving concentration and purification in prototypes while providing detailed process designs and cost analyses.
- Meanwhile, research institutions such as VITO, TNO, and the University of Twente worked on developing and scaling up advanced nanofiltration membranes for industrial applications, including the demineralization of milk whey and the purification of biobased glucose.
You might also be interested in
Acknowledgement & partners
This project is co-funded by TKI-E&I with the supplementary grant 'TKI- Toeslag' for Topconsortia for Knowledge and Innovation (TKI’s) of the Ministry of Economic Affairs and Climate Policy.
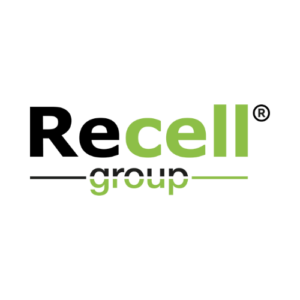
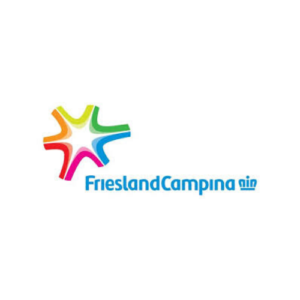
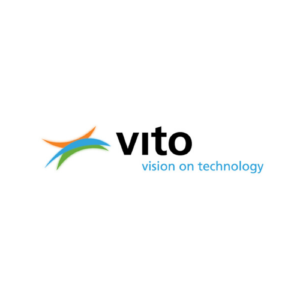
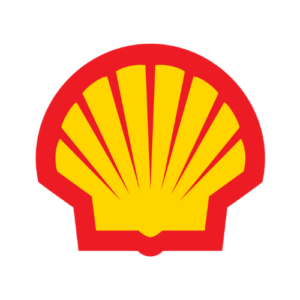
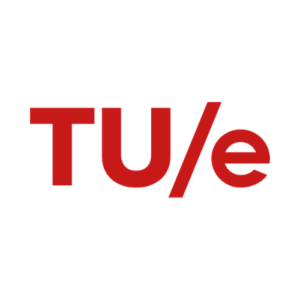
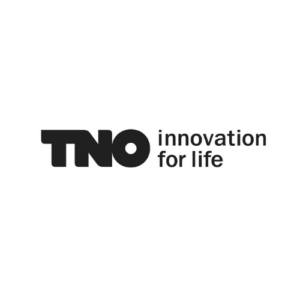
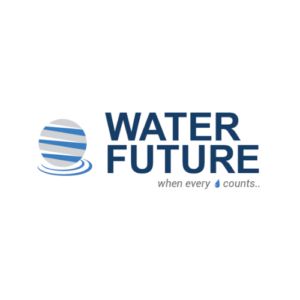
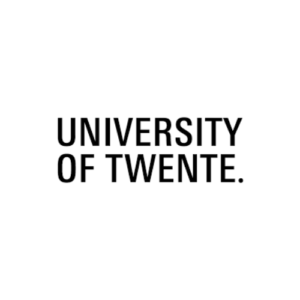
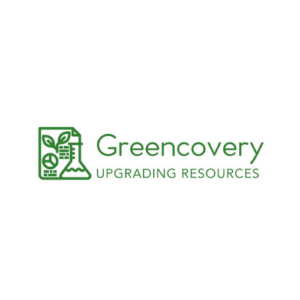
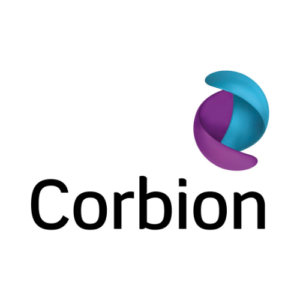
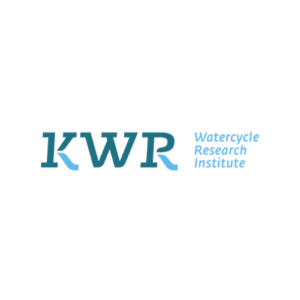