A large part of powdered formulations within the food industry is produced by spray drying. The powder properties, such as its bulk density, flowability and reconstitution behaviour, are influenced by the level of agglomeration occurring during the spray drying process. This project aimed at developing more knowledge of agglomeration mechanisms to create better guidelines to control agglomeration during spray drying to improve product quality and energy savings.
In short:
- StAgglop aimed at developing more knowledge of agglomeration mechanisms to create better guidelines to control agglomeration during spray drying to improve product quality and energy savings.
- The use of a new droplet drying platform demonstrated that improved single droplet drying approaches can be used to characterize the physical phenomena underlying the drying and agglomeration behavior of droplets during spray drying.
- Different pilot scale studies showed that nozzle position strongly affected fouling while air distribution did not affect agglomeration in the single stage spray dryer set-up used in the investigation.
- The research provides the base for predictive models and practical guidelines that help optimizing agglomeration behavior in industrial practice.
Reducing emissions by improving agglomeration control
Agglomeration during spray drying occurs mostly in the nozzle zone when a partially dried droplet collides with another partially dried droplet or with a fully dried particle or growing agglomerate. Lack of control of agglomeration negatively impacts the operational efficiency of spray dryers (e.g. due to fouling and lower production capacities) and leads to significant material losses (in the form of off-spec product) during large-scale production.
To develop knowledge-based guidelines to steer sticky behavior and agglomeration in spray drying, different studies were performed. Drying kinetics, evolution of sticky surface properties and binary particle collisions at the single droplet scale were studied by Nienke Eijkelboom in combination with pilot-scale spray drying and agglomeration studies by Anneloes van Boven, both from the Laboratory of Food Process Engineering Group from Wageningen University. The project started by jointly reviewing the state of art concerning structuring of particles during spray drying from the perspective of single droplet and pilot-scale spray drying.
Subsequently, several studies were performed also with valuable input from industrial partners Danone, dsm-firmenich, FrieslandCampina, Corbion and University of Hohenheim as additional academic partners
A new droplet drying platform
Interaction between a drying droplet and a fine particle does not always result in sticking but can also lead to merging or bouncing. Using a new droplet drying platform, realistic drying trajectories were simulated, and binary collision studies were performed. This platform enabled the mimicking of relevant droplet drying processes and the identification of collision regimes that lead to the desired sticky behavior.
It was demonstrated that improved single droplet drying approaches can be used to characterize the physical phenomena underlying the drying and agglomeration behavior of droplets during spray drying. The learnings obtained at the single droplet scale provided important new insights that can be used to steer particle agglomeration during spray drying processes.
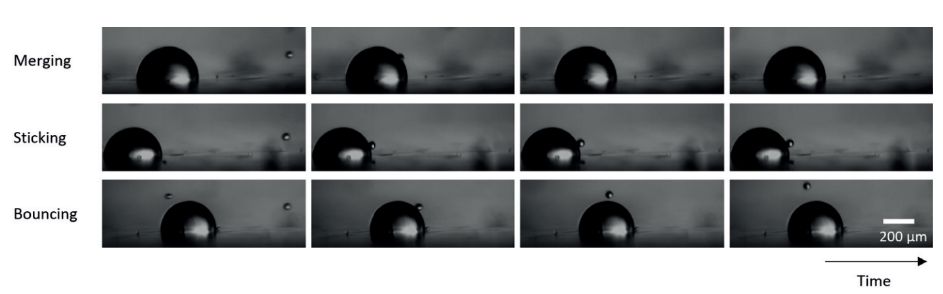
Pilot scale studies
Various factors influence primary particle formation and agglomeration ranging from the design aspects of a spray dryer to drying conditions (such as air temperatures, flow rates, atomization and dry powder dosing) and material properties of the feed material. Pilot-scale spray drying trials were performed to validate the sticking behavior by investigating agglomeration and yield upon drying of maltodextrin-protein mixtures. A systematic study was done using controlled fines dosing, inlet air and drying air temperature, where it was shown that especially fines dosing rate and the drying rate had the largest influence on the agglomeration behavior in a spray dryer. Also, a study was carried out on the effect of the air distributor design and nozzle position on operability of the pilot-scale spray dryer. Sharing expertise on CFD modeling and spray dryer design by one of the industrial partners was one of the numerous examples of direct collaboration between academic and industrial partners. The study showed that nozzle position strongly affected fouling while air distribution did not affect agglomeration in the single stage spray dryer set-up used in the investigation. These studies contributed to the development of knowledge-based guidelines to better steer particle structure formation during spray drying.
Predictive models and practical guidelines
The project was concluded with a joint investigation of both PhDs on protein addition to steer collision and agglomeration behavior at the two experimental scales. Both pea and whey protein isolate were used as an additive to a maltodextrin formulation in different ratios to study their effect on agglomeration behavior. During both binary collision and pilot-scale spray drying, the addition protein contributed to enhanced probability of sticking and thus agglomeration. These results highlight the importance of both the time at which a collision occurs, as well as the droplet composition, for optimizing the spray drying process. The research provides the base for predictive models (from single droplet experiment to spray drying) and practical guidelines that help optimizing agglomeration behavior in industrial practice.
A steppingstone to further research
Remaining challenges such as characterizing drying droplet-droplet collisions, agglomeration by fines recycling and further predictive model development (based also on prior work in the EEMS project) were identified for a follow-up research program named DRAGONS. The first project in this program, named DRAGONS Egg, started March 2023. In this project, WUR and TU/e will continue the advanced numerical modelling and experimental research efforts on spray drying at the droplet scale together with the industrial consortium partners.
Next step on the base of StAggloP and EEMS is the soon to be submitted DRAGONS Hatchling project proposal where the focus will be on the pilot and industrial scales.
You might also be interested in
Acknowledgement & partners
This project is co-funded by TKI-Energy with the supplementary grant 'TKI- Toeslag' for Topconsortia for Knowledge and Innovation (TKI’s) of the Ministry of Economic Affairs and Climate Policy.
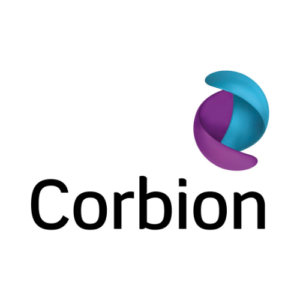
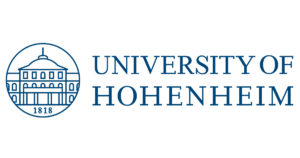
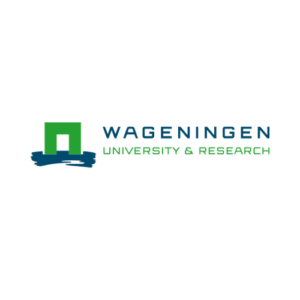
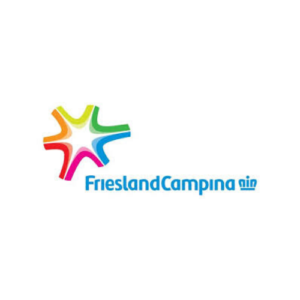
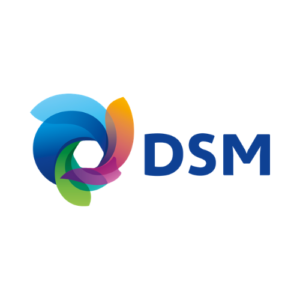
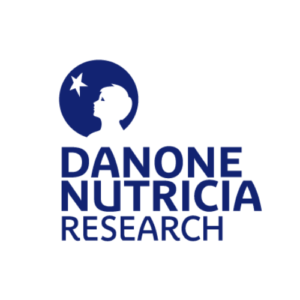