Unlocking energy efficiency and fault detection with electrical signal analysis
Electric motors and rotating equipment—such as pumps, fans, compressors, and conveyors—consume over 40% of global electricity. However, nearly one-third of this energy is lost due to malfunctions, inefficient operations, and suboptimal asset selection. Electrical Signature Analysis (ESA) has emerged as a scalable solution to address these inefficiencies.
In October 2019, the ERGO project launched the largest ESA field trial to date, aiming to assess how ESA can reduce industrial downtime and energy waste. ESA converts electrical data into valuable insights on asset health and efficiency. With non-intrusive sensor placement, the technology is well-suited for large-scale industrial applications.
Key findings
The ERGO project exceeded expectations, demonstrating that Samotics’ ESA-based monitoring system, SAM4, plays a crucial role in energy efficiency and operational reliability:
- 89% of failures in motors, transmissions, and loads were detected weeks to months before actual breakdowns.
- ESA identified operating conditions that accelerate wear and tear, helping to extend equipment lifespan.
- Samotics’ Energy Analytics platform revealed that non-optimized assets could reduce energy consumption by an average of 25.2%.
- The platform provided actionable insights into which assets could be optimized and how.
The role of digital innovation in industrial sustainability
The Copernicus Institute examined ESA in the context of twin transitions—the intersection of digitalization and decarbonization. Their research highlights that while AI and digital analytics can optimize industrial efficiency, their sustainability impact depends on how they are integrated into decision-making and operations. The study also identifies barriers such as misaligned incentives and skills gaps that must be addressed for digital tools like ESA to drive real transformation. More details can be found in their study: Digital Innovation and Sustainability Transitions.
Future outlook
ERGO’s success highlights the accuracy, scalability, and value of ESA technology in minimizing unexpected downtime and energy losses in AC motor-driven systems. Further opportunities include:
- Enhanced energy optimization by analyzing entire production systems instead of isolated assets.
- Integration with Variable Frequency Drives (VFDs) to develop intelligent, self-learning drive systems—essentially creating “VFDs with PhDs.”
More information
ArcelorMittal uses innovative predictive maintenance to reduce unplanned downtime
What is SAM4
SAM4 vs Vibration Analysis
You might also be interested in
Acknowledgement & partners
This project is co-funded by TKI-E&I with the supplementary grant 'TKI- Toeslag' for Topconsortia for Knowledge and Innovation (TKI’s) of the Ministry of Economic Affairs and Climate Policy.
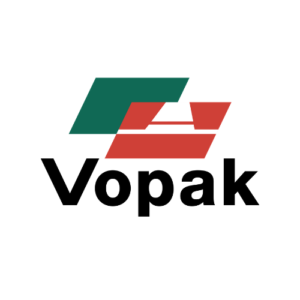
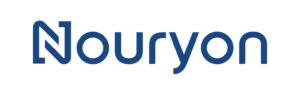
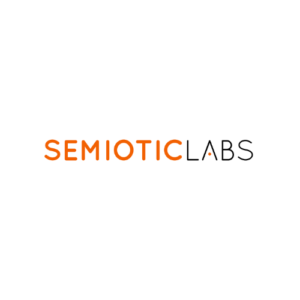
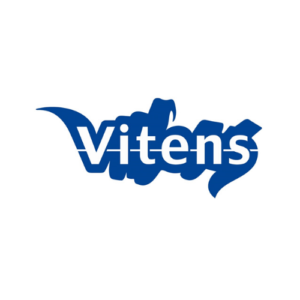
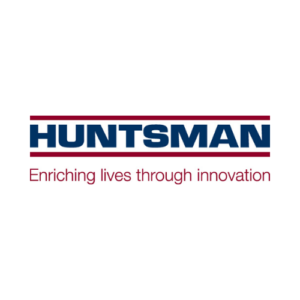
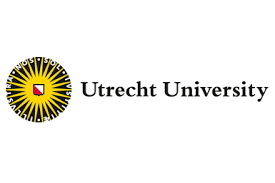
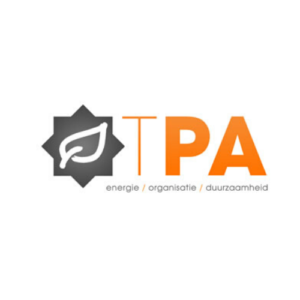