The industry needs to become more sustainable. A gigantic challenge, for a gigantic sector, with a gigantic energy demand. One of the most important sustainability routes is electrification of industrial processes. But that too is a challenge, with major consequences for the Dutch energy system. How do we still make it possible? Andreas ten Cate, program director System Integration at ISPT, outlines the route to electrification in a recent article published on Change.Inc.
From fossil fuels to electrification
In the Netherlands, the industry is a major consumer of energy. Over 40 percent of the total energy consumption in our country is dedicated to this sector. Within the industry, most energy is used for heat. Heat is used in almost every industrial process: think of pasteurizing milk, drying paper or producing iron. All these processes require high temperatures. That heat is traditionally generated with fossil fuels, like gas and coal. Conventionally, fossil fuels have offered us several advantages. Fossil energy used to be relatively cheap. Besides, it is easy to store and to supply. Therefore, it has always offered the industry security. Green energies, like wind or solar energy, are more volatile and flexible in supply. But, factories cannot just shut down their processes when energy is not available for a while, Andreas Ten Cate explains to Change.Inc.
Still, the time has come that we must move away from fossil fuels. The harmful greenhouse gas emissions associated with burning fossil fuels is a huge drawback. “Of course, there exist ways to capture and store CO2 emissions – and we will certainly need that – but if we only rely on that scenario, we will still continue to use fossil energy. A truly sustainable energy system for our industrial sector needs electrification.”
Direct and indirect electrification
Yet, electrification is easier said than done. Some industrial processes can use direct electrification, but for others this will be quite difficult. With direct electrification we can directly replace fossil fuels with green electricity. In some, more complex industrial cases, such as extracting iron in a blast furnace, this will not be possible. Because coal produces a carbon that likes to bind to oxygen, thereby serving as the perfect fuel for iron production. Electricity does not have this property, making direct electrification of iron production difficult. In this case, we turn to indirect electrification. Think for example of green hydrogen, a clean energy carrier is produced using green electricity. With green hydrogen heat can be produced in a boiler and energy can be stored with it to bridge periods of low power supply. Even processes where direct electrification is difficult, such as iron production, can be made sustainable with green hydrogen, because hydrogen also likes to react with oxygen, just like coal.
We need efficiency and flexibility
Electrifying all industrial processes therefore remains a difficult puzzle, Andreas Ten Cae says to Change. Inc. “A puzzle that is far from being laid.” An essential step, for example, is energy efficiency. Because the lower the industry’s electricity demand, the smaller the challenge will be. There is still a world to win in efficiency though: “Making your energy management more sustainable is also about reusing energy. This is possible in industry, for example by using heat pumps, vapor recompression (also a kind of heat pump) and smart ‘cascading’ of heat in factories. High-temperature processes retain residual heat at a lower temperature. That heat in turn can be used for a lower-temperature process, which in turn has residual heat left over for another process, and so on.”
Another piece of the puzzle is flexibility on the user side, Andreas Ten Cate expects. The supply of green power from solar and wind will be extremely variable. You have to be able to respond to that. Many industrial processes lend themselves well to this; they can temporarily run at a lower speed when the energy supply is low or, conversely, run at full power when there is a lot of supply. In this way, industry has a buffering effect on the energy system. “But we still have to get the hang of that and it requires a lot of investment,” Ten Cate emphasizes.
ISPT’s commitment to electrification
The Institute for Sustainable Process Technology (ISPT) is strongly committed to the electrification of the Dutch industry. Two projects illustrate these efforts par excellence. The first is the Hydrohub GigaWatt Scale Electrolyser project, in which ISPT (with partners) delivered the world’s first blueprint for a gigawatt-scale green hydrogen plant. This scale-up is important: it is the vital link between offshore wind farms and the industry’s huge energy demand,” Ten Cate says. “Another project around electrification that ISPT is overseeing is the e-Missi0n project. This project investigates how to electrify the process of steam cracking, for which at date fossil fuels are used to achieve high temperatures.
More on Andreas Ten Cate
Andreas had extensive knowledge on everything sustainable industry-related: from heat, to water to green energy – he has worked on almost every front. He has a PhD in Chemical Engineering and a background in process- and operational improvement of chemicals – like steel and aluminium. But above all, he’s curious by heart.
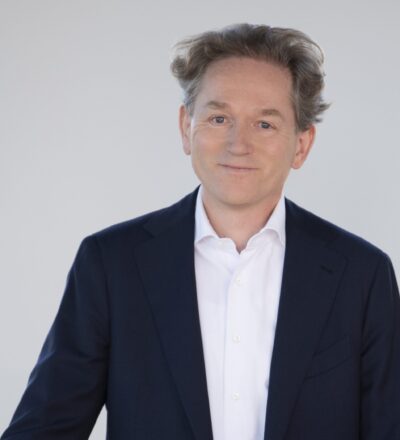