The e-Missi0n project (e-mission) aims to develop 2 technological routes that lead to the electrification of the steam cracking process to enable the production of low-carbon olefins. The project is supported by the MOOI subsidy scheme.
In short:
- In the current steam cracking process fossil fuels are used to achieve high temperatures
- Emissions for cracking are 5 million ton CO2 per year
- Out of which our industrial partners Shell and Dow emit 68%
- Therefor we need to electrify this process (e-cracking)
E-cracking can reach an emission free process
Currently, the production of olefins in large-scale cracking furnaces is a prominent source of carbon emissions. Within the Netherlands alone, the emissions for cracking are 5 million ton CO2 per year, out of which our industrial partners Shell and Dow emit 68%. In the current steam cracking process, oil gasses are incinerated to achieve the high temperatures that are required for the process.
Electricity from renewable sources is an alternative opportunity to fuel this process. By fueling the process with green electricity rather than fossil fuels, it is possible to reach an emission free process.
Activities in the MOOI-scheme
Within e-Missi0n MOOI the consortium works together to research 2 different routes that lead to the electrification of the cracking process of olefins. The 1st route is the drop-in solution, where the current process is used as a basis, with the aim to replace the current burner with an electrical equivalent. The 2nd route is the development of a completely new heating concept. The latter route is more complicated, but gives us the opportunity to get rid of, or dodge current process technological barriers
Results
With these 2 routes we aim to develop steam cracking technology that can convert the electrical energy towards heat, as well as an approach where we develop electrification technology that focuses on thermo-molecular physics. Simultaneously we aim to optimize the heat-integration of the oven section to reduce the energy footprint of the process.
The research done in the 1st route may lead to the construction and start-up of a demonstration plant in 2025, subject to investment support.
Also interesting to read
- Eerste stap richting elektrische kraker, VNCI 2021
- Dow and Shell start up electrified steam cracker unit, Chemical Engineering 2022
- Review of the molten salt technology and assessment of its potential to achieve an energy efficient heat management in a decarbonized chemical industry, de Figueiredo Luiz, D., Boon, J., Otero Rodriguez, G. & van Sint Annaland, M., 15 October 2024, In: Chemical Engineering Journal
You might also be interested in
Acknowledgement & partners
This project is co-funded with subsidy from the Topsector Energy by the Ministry of Economic Affairs and Climate Policy.
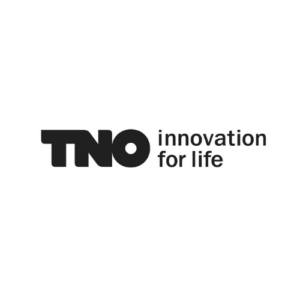
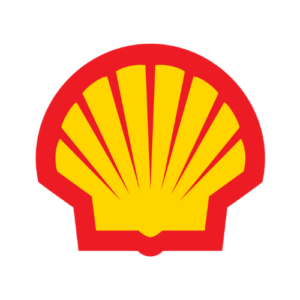
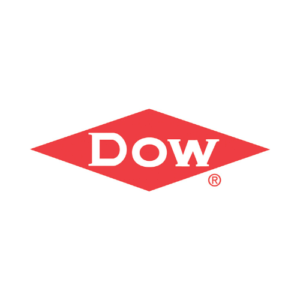
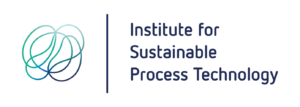