Conductive drying shows lower energy consumption, operating expenditures and capital expenditure than conventional spray drying, but conclusions may ultimately vary per product. The Thin Film Drying project resulted in guidelines for which conductive drying method to select.
In short
- Conductive drying technologies show lower energy consumption
- This led to new guidelines for which drying method to select
Model development for conductive thin film drying process
We investigated operational parameters of different thin film technologies and analysed different samples. We collected information on the skin formation process and its relation to drying behaviour, powder properties and activity loss of a model component (e.g. enzyme) using in- and off-line analytical tools.
Laboratory-scale drying experiments with custom-built drying devices were carried out to understand the degradation and formation dynamics of product quality parameters and to characterise kinetics during conductive drying processes. Additionally, an experimental pilot scale programme and techno-economic assessment were carried out to compare and study the different conductive drying technologies in terms of product quality, energy consumption and costs.
New drying methods assessed
A techno-economic assessment of different conductive drying technologies is made. Energy use was compared on the basis of energy use per ton water removed. It is concluded that conductive drying technologies show lower energy consumption, operating expenditures and capital expenditure than conventional spray drying, but conclusions may ultimately vary per product. The final technology choice for making a product depends largely on the ability of a process to dry the raw materials to the desired product specifications.
Pilot-scale experiments were carried out to compare the quality (colour and flavour) of tomato powders prepared by four pilot-scale dryers available at different locations, namely a vacuum drum dryer (VDD), a drum dryer (DD), an agitated thin film dryer (ATFD) and a refractance window dryer (RWD).
Lower CAPEX/OPEX for conductive drying technologies
It is concluded that conductive drying technologies show lower energy consumption, operating expenditures and capital expenditure than conventional spray drying, but conclusions may ultimately vary per product. By combining the techno-economic assessment and the experimental pilot-scale results, guidelines for selecting an appropriate conductive drying method for a (tomato-based) product are formulated. The final technology choice for making a product depends largely on the ability of a process to dry the raw materials to the desired product specifications.
Learn more on our Drying & Dewatering Program or contact Peter de Jong.
You might also be interested in
Acknowledgement & partners
This project is co-funded by TKI-E&I with the supplementary grant 'TKI- Toeslag' for Topconsortia for Knowledge and Innovation (TKI’s) of the Ministry of Economic Affairs and Climate Policy.
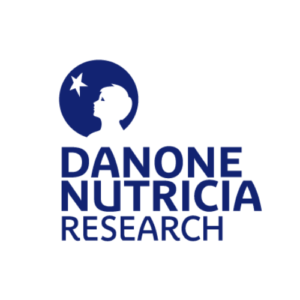
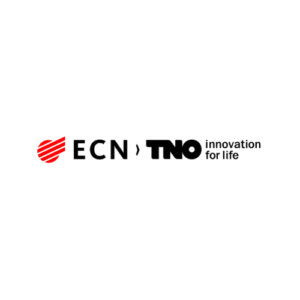
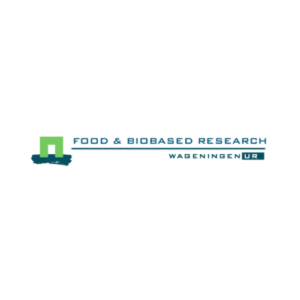
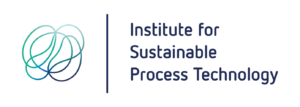
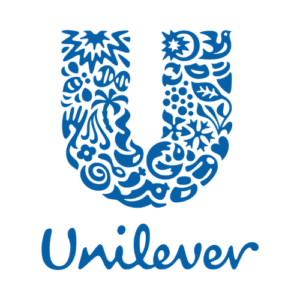