Spray drying is used in the food industry to transform food and dairy products into powders, preserving taste, smell, and all nutritional aspects. It also guarantees product quality for an extended period of time and facilitates easy transport of products. However, spray drying is an energy intensive technology. It consumes 15% of the overall energy consumption within the Dutch industry. The Engender project took the next step in low-energy drying of food and other high-value products. How? By developing the Radial Multizone Dryer (RMD) technology at the pilot scale.
In short:
- Engender aimed to realize a breakthrough in drying of food
- A new drying technology was used: Radial Multizone Dryer (RMD)
- Expected energy savings are estimated up to 30%
Radial Multizone Dryer (RMD)
The Engender project aimed to realize a breakthrough in drying food ingredient materials using a new compact drying technology: the Radial Multizone Dryer (RMD). The RMD combines high-G and multizone operation to intensify spray drying and provide a cost and energy efficient spray drying solution. The existing pilot plant unit was used to carry out spray drying experiments. The experiments were aimed at confirming the flexibility of the RMD technology and to optimize the operating parameters and design details. Through extensive testing and refinement, the team addressed challenges related to scalability, stability, and product quality.
One of the key innovations introduced was the optimization of countercurrent flows using Computational Fluid Dynamics (CFD) simulations. These modifications not only enhanced energy efficiency but also improved product quality by controlling droplet and particle size distribution.
Compared to traditional spray drying technologies, the RMD technology aims to achieve:
- Reduced equipment footprint for the same drying capacity and associated reduction in Capex and Opex (equipment size reduced by at least one order of magnitude).
- Improved energy efficiency of approximately 30%.
- Significant reduction in air consumption and exhaust air. Such exhaust air, e.g. from spray drying of flavours or fragrances, can be highly contaminated andn requires treatment. A reduction of the drying air quantity, will reduce efforts in exhaust air treatment.
- Reduced water consumption in the cleaning process (CIP) due to the lower footprint (less equipment surface to clean).
- Same or improved product quality. The manufacturing costs per kilogram of product remaining at least cost-neutral compared to standard spray drying processes.
Cost and energy efficient spray drying solution
Efficient drying was achieved by combining radial multizone and high-G operation. Radial multi-zone operation allowed hot air to be supplied to the radially central zone of the chamber where the droplets were injected, while mild temperature air was supplied to the periphery where the particles were recovered.
High-G operation was achieved by utilizing vortex chamber technology. Mild temperature air was injected through a number of vortex chambers to generate rotational motion and control axial motion in the drying chamber. Droplets injected into the chamber underwent fast initial drying upon contact with the hot air. The droplets were then rapidly evacuated to the mild temperature periphery for final drying and recovery.
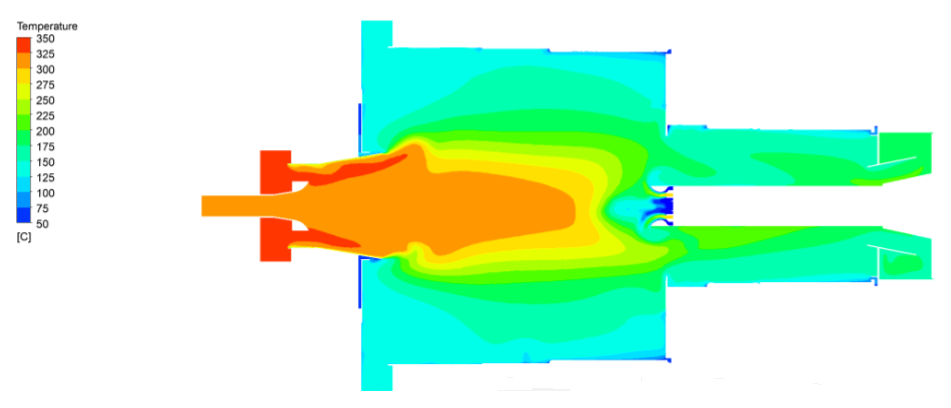
A new simplified design necessary for commercialization
The operating principle was found to be more energy-efficient and the savings-etimate was deemed realistic. However, despite significant progress, challenges remain. Particularly regarding scale-up and equipment simplification. The complexity of the current design necessitates collaboration with industrial equipment suppliers to develop a more streamlined solution. A recommendation was made to use the available knowledge to create a simpler design. Additionally, ensuring product quality and minimizing exposure to hot air remain focal points for future development.
Looking ahead, the Engender project marks a critical step towards commercializing energy-efficient spray drying technology. The focus is on scaling up and refining the design based on project learnings. The journey towards a more sustainable and cost-effective future for the food industry continues.
The project executed validation of several model systems. Engender’s long-term goal is to scale up the Compact Energy-Efficient Dryer technology for implementation by 2031.
You might also be interested in
Acknowledgement & partners
This project is co-funded by TKI-Energy with the supplementary grant 'TKI- Toeslag' for Topconsortia for Knowledge and Innovation (TKI’s) of the Ministry of Economic Affairs and Climate Policy.
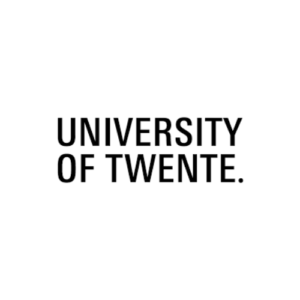
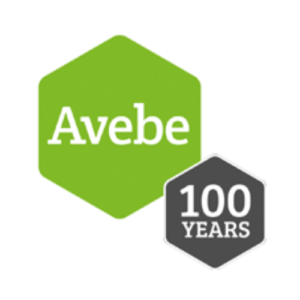
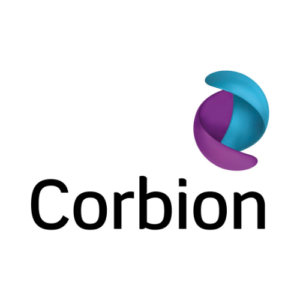
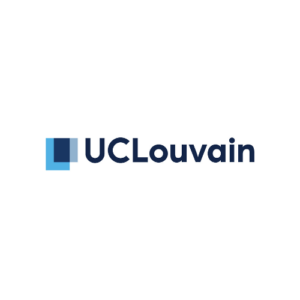
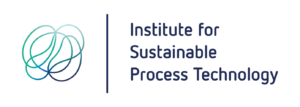
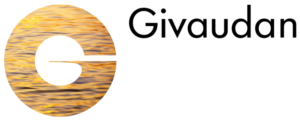