Industry must reduce its greenhouse gas emissions to limit global warming. Technology to capture CO2 is in place. This can be introduced competitively if the captured CO2 can be put to use. Methanol production from CO2 off-gasses from waste could provide part of the answer. This comes with a big if: existing CO2-to-methanol pathways should become more efficient. That is what the PROVE IT project intends to realize within the next three years, starting from October 2021.
Methanol (MeOH) is a much used chemical building-block. The market reached 7,5 Mton in 2017 in Europe. This equals approximately 10 Mton of potential CO2 savings per year. Methanol is widely applied in the Netherlands and elsewhere for the production of various materials such as acetic acid, polymers and fuel additive. The necessary MeOH is currently mainly produced overseas from natural gas. It is subsequently imported into Europe. Present production technologies were developed during the petrochemical era. Methanol production directly from CO2 was held back for decades by inconsistent production and capture of the building blocks for this process.
Sustainable carbon life-cycle
Wouldn’t it be better to produce this methanol locally with industry off-gassed CO2 and added hydrogen gas? Sustainable, direct CO2-to-methanol conversion technologies have already been developed as proof-of-concept. Now is the time to tweak these technologies into proper off-gas based production technology.
Wim de Jong, advisor market and strategy at Twence, the inter-communal circular economy focused waste-to-energy company in Twente: “We consider this to be a very promising way to re-use CO2. Methanol is already a bulk commodity. At the right price, there is a guarantee for sales.” Riaan Schmuhl, Program Manager Circular Carbon at Nobian in Hengelo, adds: “PROVE IT will take the first steps in proving the technical feasibility of the production of methanol from CO2 waste gas. We are excited to learn from the project and to develop this technology up to full scale production.”
Improving efficiency
PROVE IT is set out to enable a major step towards a sustainable carbon life-cycle within the chemical industry. A first result area explores the availability of carbon sources and assesses the development of demand and value of its derivatives for CO2-to-methanol production. The answers will support decision making on investment to scaling up this new technology. It will also help policy makers to recognize the need to adjust incentives, penalties and regulations. The second result area consists of system analysis and cost analysis to define the optimized catalyst productivity, selectivity and lifetime for producing methanol from an off-gas CO2 source.
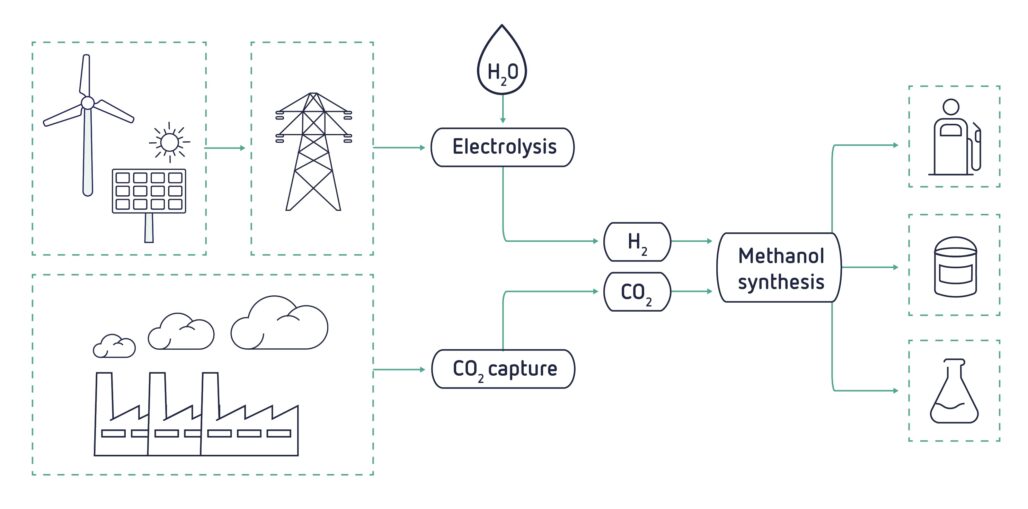
European Sustainability Agenda
This fits perfectly to the national and European sustainability agendas as laid down in the MOOI and MMIP6 / IKIA closing industrial chains CO2 emission reduction target of 35 Mton CO2 per year for industry. The theoretical groundwork for improving overall process efficiency has already been laid. PROVE IT will focus on engineering to convert CO2 to Methanol for later manufacturing, operation and upscaling.
Stably activated catalyst
Two key technical issues have to be overcome. Long-term stability of the catalyst for CO2 hydrogenation to MeOH with practical CO2 point sources will have to be demonstrated. Apart from that, tools will be developed to predict operational stability on an even longer term. Furthermore, the process of CO2 hydrogenation generates a lot of water and reaction heat. This causes deactivation of the catalyst because of hydrothermal sintering. There is no doubt that both hurdles can be jumped, but commercial viability demands satisfying conversion and selectivity levels. The most anticipated aspect will therefore be cost-effectiveness.
Multivariable optimization
For that purpose the reaction conditions and process design need to be optimized. This will be done in an approach using data from high-throughput-experimentation with process simulation. This enables assessment of catalyst deactivation and activity over time with varying process conditions, feed-streams and recycle composition. This approach will lead to an overarching process model that contains a kinetic model combined with a model for catalyst deactivation. In this way, multivariable optimization can be realized to bring the project to its next phase: pilot operation. “We are curious for the research results, so we are able to make a careful decision about building this pilot installation”, De Jong comments.
Impact potential
The project result points the way in which this conversion technology can bring about change. The catalytic reactor developed in the project will have potential applications at CO2 point sources in general, in the port of Rotterdam and other major industrial areas. This also asks for broader carbon value chain assessment: a match of feedstocks and end products, calculation of the impact potential, and the development of a roadmap to ensure adoption of the most promising options.
Social economic impact
The start will, however, be made in Twente. Twence’s CO2-rich industrial off-gasses are the basis for the project’s lab tests. De Jong: “We have already established that the CO2 captured and liquefied at Twence has the right quality for the conversion process.” A catalytic reactor at Twence will be tailored to the research outcomes. PROVE IT uses renewable energy to do this, making it the first carbon-based methanol production from renewable energy.
A large regional market for this sustainably made methanol is guaranteed in and nearby Twente, which increases the chances of success. If successful, the clean-technology-based and systems-integrated economic ecosystem in Twente would benefit. De Jong: “A regional CO2-to-methanol plant would support many research and development jobs. Building a pilot and eventual scale-up would boost the regional hightech sector to employ hundreds of people.”
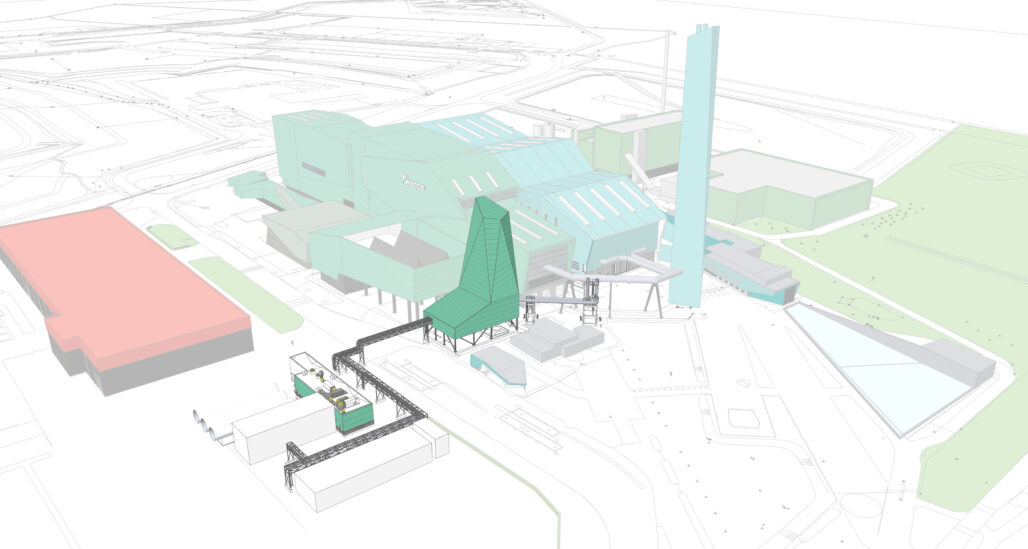
Nobian will be an important customer for the methanol produced. Marco Waas, VP/Director RD&T, Sustainability at Nobian: “As a market leader in the production of essential chemicals it is our ambition to ‘Grow Greener Together’ with our customers and energy suppliers, such as Twence. PROVE IT is a key project in realizing this ambition, a CO2 free value chain and stimulating circularity. Developing alternative means to secure the production of green methanol from waste helps to reduce our CO2 footprint of our chloromethane value chain.
Complete supply chain
“The present consortium suits perfectly to existing collaborations, which is an important condition for future partnerships once this technology becomes operational”, De Jong continues. Almost the entire supply chain is present in the Netherlands and has teamed up in PROVE IT: methanol-users, technology developers, CO2 off-gas producers and energy producers. System integration researchers and catalytic R&D businesses assist them.
Project Partners
The PROducts of Value from various CO2 sources, Enabled by Integrating Technologies (PROVE IT) consortium consists of Twence, Nobian as one of the leading parties in green hydrogen, Avantium as innovator in catalytic R&D, DAREL, Metabolic, Suster and the University of Twente as knowledge providers with excellent track records and relevant know-how in the field. Clariant is linked as an associated consortium member to fulfil its leading role as catalyst provider.
The PROVE IT project is supported by the MOOI (Mission-driven Research, Development and Innovation subsidy) subsidy scheme.
Acknowledgement
This project is co-funded with subsidy from the Topsector Energy by the Ministry of Economic Affairs and Climate Policy