Circularity is the cornerstone of a sustainable future. In a circular economy, resources are kept in use for as long as possible while maximum value is obtained from their usage. Then, at the end of their service life, materials are recovered and regenerated. What is waste for one factory, might be a highly valuable resource for the other. In establishing the future circular economy, the relevance of circularity in the industry – and in particular the process industry – cannot be underestimated.
What is circularity?
In our contemporary society, the majority of resources are still used for products that we use for a short period of time, and then discard. There is widespread agreement that this linear system based on a ‘take-make-waste’-model is no longer sustainable. A transition to circular use of materials, water, nutrients, and carbon, combined with minimal loss of natural resources, is necessary. Only then can the climate of our planet recover.
This means we need to transition to a circular economy, in which resources are kept in use for as long as possible while obtaining maximum value from their usage. This means that at the end of their life-cycle, materials are recovered and regenerated, contributing to a more sustainable future. At ISPT, we believe that circularity is the cornerstone of a sustainable economy, and we are committed to promoting the responsible use of materials through the principles of circularity. In short:
- To achieve the goals of the Dutch and Paris Climate Agreements, the world needs to transition to a circular economy;
- Product manufacturers must take the reuse of their products into account during the design;
- Consumers contribute to a circular economy by using items for a longer time, repairing them, or taking them to thrift stores.
ISPT envisions a waste-free economy in which products and raw materials are either recycled or reused. In this new economy we have to transform our value chains. For instance, carbon and plastics will no longer be waste products but valuable resources. Together with our partners we’re making circularity a reality. We are working on feasible and innovative solutions that will lead to full circularity by 2050.
A circular system builds a future in which the Netherlands can be frontrunner in new technologies
Tjeerd Jongsma – director ISPT
What is the challenge?
The challenge lies in achieving circularity at multiple levels. Ultimately, our focus is on developing the technology required for establishing a truly circular economy. When products at the end of their lifespan are chemically degraded, the constituting molecules can re-enter the product cycle. Achieving this requires innovation in technology for production, recycling and re-use, powered solely by renewable energy. It often requires close cooperation between sectors of industry that until now have been operating independently.
Climate
• The Circularity Gap Report presented by Davos reveals that only slightly over 9 percent of raw materials in the global economy are being recycled. The report highlights that these raw materials include construction materials, food for human consumption, and raw materials for electrical appliances.
• A report by Circle Economy shows us that the current linear economy model is not sustainable anymore and that there is a need to focus on reusing raw materials. The report underlines that a shift towards a circular economy is vital to tackle climate change and resource overuse.
• The CEO of the World Business Council for Sustainable Development, Peter Bakker, regards the report as a promising step in understanding global progress towards a circular economy.
Industry
A circular economy also has implications for industry. In a circular economy, there is less demand for new products, and therefore less demand for raw materials. This leads to fewer CO2 emissions throughout the industry production chain. But to become truly circular, industry itself must also take action. For example, industry can:
- Design products to last longer. This can be done through better repairability, sturdier design and reusability of individual parts.
- High-quality recycling of raw materials from end-of-life products. With high-quality recycling, the raw materials have the same or even better quality after recycling.
- Commit to renewable raw materials. These are raw materials whose supply can be restored in a short period of time. For example, we can use residual streams from agriculture as raw materials in the chemical industry, instead of petroleum.
Closing the loop: a fundamentally different approach
In the field of chemicals and plastics, ultimate circularity lies at the molecular level. When products at the end of their lifespan are chemically degraded, the constituting molecules can re-enter the product cycle. This requires new technology for production, recycling and re-use, powered by renewable energy.
To achieve this we need everyone. And that is a fundamentally different approach. It’s no longer about separate process innovations, but about a system innovation in which we close the chain together.
In 10 steps towards circular business models
Circular business models have proven their viability and are now demonstrating their effectiveness in practice.
- Circular sourcing: Replace finite resources/materials in the production process with renewable, biobased, or recycled materials.
- Sustainable design: Design products in a way that enables effective disassembly, reuse, repair, and upcycling.
- Efficient resource utilization: Optimize the use of raw materials/resources and minimize waste in the production process.
- Product-as-a-service: Provide a service where previously only the product was sold; extend the product lifecycle through repurposing at the end of use.
- Sharing/virtualization: Share sustainable assets such as cars, rooms, appliances, and devices, and digitize products to extend their lifespan.
- Use/maintenance optimization: Improve product performance/efficiency and extend lifespan through proper maintenance.
- Reuse/redistribution: Purchase and sale of second-hand and used products.
- Renovation/remanufacturing: Remanufacture products or components for a new use instead of downcycling.
- Industrial symbiosis/Recycling from production: Waste or by-products from production become the basis for another product.
- Recycling from use: Recycle discarded materials after the end of their consumption.
What role does (process) industry play in sustainability and circularity?
In 2020, of the total amount of greenhouse gases, 32 percent were emitted by industry, 20 percent by the electricity sector, 19 percent by the mobility sector (domestic traffic and transport), 16 percent by agriculture and 13 percent by the built environment (due to burning natural gas for space heating).
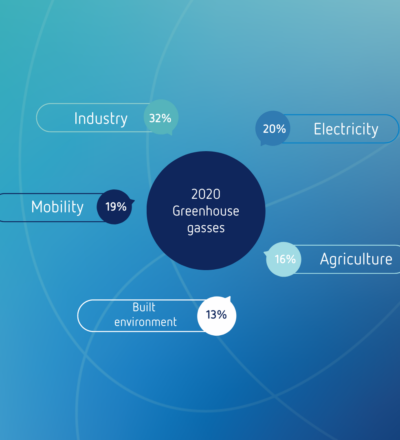
These are the five sectors distinguished in the Dutch Climate Accord presented on June 28, 2019. The (process) industry is undeniably a significant sector with immense potential for progress and improvement.
In a circular economy, waste becomes a valuable resource. Nearly all products used in the future are repeatedly reused in a circular economy. When a product is broken, it is repaired, and if it cannot be repaired, new products are made from the old ones. The traditional linear model of producing, consuming, and disposing no longer applies.
A well-functioning circular economy relies not only on the government and the business sector, but also on consumers who must make sustainable product choices the new norm. Consumers can also contribute to a circular economy by using their belongings for longer, repairing them, or donating them to second-hand stores. The government aims to encourage such behavior by incorporating circular economy principles into education and running campaigns.
The Dutch Climate Agreement
In less than 30 years, the Dutch industry needs to be fully circular and emit almost no greenhouse gases, states the Dutch Climate Agreement for 2050. In short, this means that:
- Our factories will run on sustainable electricity from solar and wind, or energy from geothermal sources, hydrogen, and biogas;
- The raw materials will come from biomass, residual streams, and gases;
- The industry will use the excess heat itself or supply it to horticulture, buildings, and homes;
- The industry will not only be an energy user but also a producer and energy buffer.
By 2030, the industry must already significantly reduce CO2 emissions. This is an intermediate step towards full sustainability. Many of the new production methods are still in their infancy and are too expensive. Companies are investing in these innovations themselves. There is also subsidy available to kickstart the development. This way, the industry can become the most CO2-efficient industry in Europe without jeopardizing its international competitive position.
Paris Climate Agreement
To achieve the goals of the Paris Climate Agreement, the world needs to transition to a circular economy. It is stated that a circular economy can reduce greenhouse gas emissions by approximately 20% and contribute to the commitments of the Paris Agreement. The transition to a circular economy is therefore necessary for a climate-neutral world by 2050.
- Climate change is one of the greatest challenges of our time;
- A circular economy can play a crucial role in addressing this crisis;
- A circular economy promotes smarter and more efficient use of resources to minimize waste and pollution;
- It involves sharing possessions, such as cars, and smartly reusing materials and primary resources;
- Circular practices go beyond waste recycling and involve changes throughout the entire supply chain;
- The transition to a circular economy contributes to a sustainable economy and a better living environment;
- Innovation and collaboration are essential in this transition;
ISPT’s vision
At ISPT, we believe that achieving sustainability and circulairity in the industry is a collective task. Instead of generic measures by the government, such as carbon pricing, we will establish customized agreements. What investments will the industry make to achieve CO2 reduction? These are significant investments that require careful consideration and planning.
At operations level
Therefore, many ISPT projects are aimed at achieving circularity at an operations level, focusing on the efficient use of resources and energy. An important aspect here is the prevention, reduction and recycling of waste. Another is the sustainable generation and use of heat, for instance in the concept of ‘circular heat’. The idea here is to cycle heat through a closed pipeline among a group of factories. Each of these applies heat pumps powered with renewable energy, to realise the temperatures required for their process and to return excess heat to the pipeline at the right temperature.
Across the value chain
Another important effort of ISPT concerns circularity across the value chain. For instance, in the field of chemicals and plastics, ultimate circularity lies at the molecular level. When products at the end of their lifespan are chemically degraded, the constituting molecules can re-enter the product cycle. Achieving this requires innovation in technology for production, recycling and re-use, powered solely by renewable energy. It often requires close cooperation between sectors of industry that until now have been operating independently. Closing the carbon cycle in the Steel2Chemicals project is a prime example of this.
A second example of achieving circularity across the value chain concerns closing the nutrient cycle in food production and use. ISPT is involved in an analysis of nutritional value and cost, zooming in on N, P, and K nutrients, proteins and micronutrients, and considering all aspects – from the depletion of agricultural acres to the processing of food and the collection of food waste. Together with, amongst others, the fertilizer and food industries, we aim to establish a sound scientific foundation for achieving circularity in this complex matter.
Our efforts
Circularity of plastics
The widespread use of plastics in our modern world has brought about tremendous benefits, but also significant environmental concerns, especially with plastic waste littering our planet. In response to this issue, the Circular Plastics Initiative (CPI) has set out on a mission to promote the transition to circularity in plastics at an industrial scale. Because as a society, we need to rethink plastic. It is far too valuable to be treated as waste. And it can serve as the feedstock for circularity. This calls for concerted action, in particular, to tackle plastic waste and ensure its recycling.
To solve these issues, the CPI addresses the entire plastics value chain, including technological, logistic, and societal challenges, with the ultimate goal of moving away from the current linear system of production based on fossil fuels, to a closed circular system where plastics are made from recycled materials and CO2 emissions are reduced. To achieve this vision, the CPI has developed an interactive Circular Plastics Roadmap, which outlines necessary steps for a circular future. Download the roadmap to learn more about how plastics can be used responsibly in a sustainable future.
The mission of the Circular Plastics Initiative (CPI) is to boost circularity in plastics on an industrial scale. We address the entire value chain from an international perspective and focus on the technological, logistic, and societal challenges lying ahead. In 2021 the Circular Plastics Initiative released its Circular Plastics Roadmap, which it developed in collaboration with experts from industry and academia.
The Circular Plastics Roadmap isn’t just a timeline with milestones. It also sets out a vision for the future and shows how it can be realized. While the CPI underlines the enormous value of plastic in our society, it also acknowledges the reality of litter, landfills, and the environmental impact that plastics have. Our ultimate goal is a future in which we have moved from a linear system of production based on fossil fuels to one based around a closed circle. In that circle, plastics is made from recycled materials, and CO2 emissions are drastically reduced.
In order to promote the circularity of plastics on an industrial scale, we need to work more effectively together. That means understanding each other’s roles, so that each step of the chain can take into account the previous and the next steps. So far, the willingness to collaborate in the field of circular plastics is great. This is evidenced by the enthusiasm with which parties in the value chain are joining the Circular Plastics Initiative (CPI) and engaging with each other. Every year, the CPI program organizes the Circular Plastics Conference to facilitate the industry, academia, knowledge institutions and SMEs to come together and discuss the next steps in moving towards a fully circular plastics value chain.
- The CPI aims to transition to circularity in plastics at an industrial scale to address environmental concerns and promote responsible use of plastics.
- The Circular Plastics Roadmap outlines the necessary steps to create a future where plastics are made from recycled materials and CO2 emissions are reduced.
- The roadmap sets a vision for a closed circular system of plastic production, acknowledging the value of plastics while addressing litter and environmental impact.
- Collaboration and understanding of each stakeholder’s role in the plastics value chain are key to effectively promoting circularity, demonstrated by the participation in the CPI and the annual Circular Plastics Conference.
Circularity of carbon
Carbon serves as the backbone of our contemporary industry. However, the release of CO2 into the atmosphere is causing damaging effects on the global climate. Even as visionaries continue to create extraordinary solutions for the carbon capture, and storage, the process industry needs other energy sources than carbon, as well as for alternative (non-fossil) carbon feedstock. How do we transform carbon from single use to circular use without CO2 emissions, at low cost and on an industrial scale? In the Circular Carbon Program we’re developing viable pathways for managing and reducing emissions in carbon intensive industries.
In the Circular Carbon Program we consider 3 alternative carbon sources as feedstock:
- Biomass (renewables)
- CO2 from the atmosphere
- Recycled carbon from waste streams
Circularity of heat
Another integral part of Circularity is addressed in our Heat program. Its mission is to accelerate the development and application of sustainable heat and heat-integration technologies that enable the transition to 100% CO2-free industrial heating, in line with the targets lined out in the Climate Agreement.
At the moment, Heat is the largest energy consumer for a number of companies in various sectors, including agro-food, paper, chemical, horticultural, and food. In order to achieve the targets for 2030 and 2050, it is crucial to exchange and jointly build up knowledge and experiences, and share the results. The Heat program offers companies the opportunity to collaborate, share their knowledge, ambition, and experience, and explore where they can reinforce each other in developing innovative sustainable heating technologies.
In accordance with the Mission-driven Multi-Year Innovation Program (MMIP) of the Topsector Energy, the cluster focuses on:
- Heat reuse, upgrading and storage;
- System concepts for heat and cold;
- Maximizing process efficiency;
- Deep and ultra-deep geothermal energy;
- The use of climate-neutral fuels.
To tackle the vast challenge of this transition, the Institute for Sustainable Process Technology has taken the initiative for a nationally supported cross-sectoral Heat Integration Platform, in which innovation and practice are actively linked. Join us on this journey towards a sustainable future for industrial heating, and let’s work together to achieve a fully carbon-neutral heat supply for all temperatures by 2050.
Separations for Circularity
The program Separations for Circularity is committed to driving a radical change in the process industry. The goal is to transition the industry to a circular economy and reduce its reliance on fossil fuels, while also minimizing discharge and lowering carbon and water footprints.
- Accelerate the collaborative development of radically innovative technologies for the separation and treatment of fluids;
- Ensure continuity of industrial operations in a changing environment;
- Striving for a carbon-neutral and circular industry with a reduced reliance on fossil fuels.
We believe that a focus on intensification and electrification of the separation and treatment of liquids and gases, leading to energy-efficient production and the recovery and reuse of valuable components.
The program focuses on membrane and affinity-based separations, alternative driving force-based separations, integrated fluid treatment and conversion, as well as water reuse and resource recovery. We are developing versatile platform technologies that are cost-effective, robust, and future-proof, with the aim of enabling at least a 49% reduction in CO2 emissions by 2030 in comparison to 1990, as set forth in the central goal of the Climate Agreement by the Dutch government.
By bridging science to practice in a collaborative development with industry, we aim to accelerate the actual application of these technologies. Join us on this journey towards a sustainable future for the process industry.
Paths to accelerate
The big question lies in what path should we take moving forward. The Dutch government is set to make ‘principle agreements’ with the 20 largest industrial emitters in the Netherlands. These agreements are expected to be in place by the end of 2023. This approach aims to achieve a better balance of responsibility between the government and the industry.
ISPT hopes that these agreements will lead to concrete transformations in the Dutch industry, resulting in actual circular systems. It doesn’t have to be fully circular all at once, but the interventions should contribute to a complete circular system. By doing so, we choose long-term sustainable solutions and build the future of the Netherlands as a frontrunner in new technologies.
The above process should result in concrete agreements, and ISPT has full confidence in that. The business sector can use its expertise to determine which interventions are feasible and which are not. The government can impartially assess the interventions that lead to CO2 reduction in the supply chain. Both parties can come together through constructive dialogue.
The Ministry of Economic Affairs and Climate Policy (EZK) conducts the assessment using the Carbon Transition Model. This model has been developed by ISPT in collaboration with the industry and NGOs. It calculates the CO2 emissions throughout the supply chain and assesses whether an intervention contributes to CO2 reduction across the chain. We are proud that ISPT’s Carbon Transition Model contributes to informed decision-making and facilitates a constructive dialogue between the government and the industry.