26 kilograms. That is the average clothing consumption per person annually. With clothing sales growing by over 40%, the EU textile industry faces growing sustainability challenges. The increased use of cheaper polyester-cotton blends leads to increased resource consumption and waste. Within the TEXPOWER consortium, we address these issues by developing a transparent, circular polycotton textile value chain for a sustainable industry in the Netherlands.
In short:
- The blend of polyester and cotton (polycotton) is the most dominantly used composition in the current clothing industry
- This complex waste stream is expected to increase with the recent increased use of polycotton and the ban on incineration of clothing
- The goal of TEXPOWER is to enable and create a transparent, circular polycotton textile value chain
The need for circularity in textiles
The growing consumption of clothing in the EU is largely driven by the lower prices at which (fast) fashion is delivered to consumers. These reduced costs are achieved partly by using cheaper synthetic materials, often blended with cotton fibers. The blend of polyester and cotton (polycotton) is the most dominant used blend in the clothing industry. However, this sector faces a significant sustainability challenge due to the increasing demand for primary resources such as water and crude oil. As the use of these textiles rises, so does the generation of waste. In addition, it will be prohibited to incinerate unsold clothing, forcing strategies to make these products circular.
The goal of the TEXPOWER consortium is to enable a transparent, circular polycotton textile value chain that can be implemented for the future-proof earning capacity of the Netherlands.
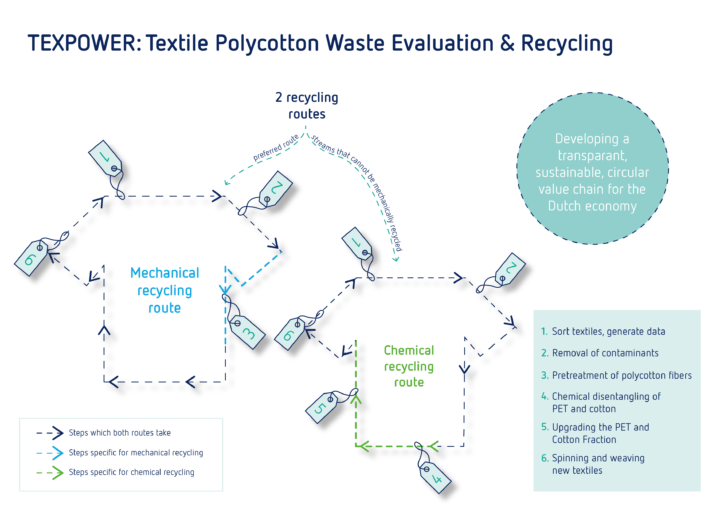
TEXPOWER: a transparant circular polycotton textile value chain
A group of key partners has been assembled to shape a circular value chain and collaboratively develop solutions: CELLiCON, DPI – Shaping polymer innovation (as coordinator and on behalf of CPI, together with ISPT), Enschede Textielstad, Frankenhuis, KringCoop, SaXcell, Hogeschool Saxion, Spinning Jenny en Textile Fiber Boost.
To reach our goals, we will develop:
- accurate and efficient identification, sorting and data processing techniques
- contaminant removal techniques
- techniques to extend or strengthen fibers during mechanical recycling
- a unique polycotton separation technology
- effective processing of polyester into spinnable fibers, upgrading cellulose pulp into spinnable fibers, and spinning polycotton yarns that can be woven into functional textiles.
Mechanical recycling will be applied where possible. Where this is not feasible, chemical recycling will be used.
New insights and techniques
This project aims to significantly improve the mechanical recycling of polycotton through several strategies. These include more specific sorting of mechanically recyclable textiles, improving the fiberizing process to extend fiber length, chemically treating the textiles to preserve fibre length during fiberizing, and introducing spinning and weaving innovations that enable a wider varietyof fibers to be spun and woven.
With these new insights and techniques, it will be possible to mechanically recycle 5-20% of polycotton. The chemical recycling of polycotton involves chemically separating the polyester fraction, which also produces a cellulose fraction. These fractions are then processed into fibers that are spun. This creates a closed system (fibre-to-fibre recycling). By 2030, it is expected that 25-37% of textiles (including polycotton) can be recycled in this way, in combination with mechanical recycling.
What we do
TEXPOWER will deliver:
- New identification, sorting, and data processing techniques that ensure faster, more accurate, and cost-effective identification and sorting of textiles, as well as the generation and processing of data for necessary reports.
- Improved and mechanized techniques for quickly and efficiently removing zippers, buttons, etc.
- Enhanced and scaled-up pretreatment techniques for polycotton textiles for mechanical recycling, resulting in longer fibers.
- Treatment techniques for polycotton to remove specific contaminants (elastane, nylon, acrylic, PFAS, etc.).
- A unique separation technology for polycotton, splitting polyester and cellulose. The combination of processes developed and applied in this project results in streams of polyester and cellulose products optimized for further processing.
- Polyester from chemical separation proven to be processable into rPET for textile yarn using existing techniques.
- Pilot-scale chemical processing of cellulose pulp, producing cellulose fibers suitable for spinning into yarn.
- New spinning and weaving techniques and insights to process mechanically and chemically recycled fibers into yarn and functional textiles with a quality comparable to virgin materials, resulting in market-applicable fabrics.
Sustainable textiles in the Circular Plastics Initiative
With TEXPOWER the Circular Plastics Initiative has entered a new era, by broadening our impact towards sustainable use of plastics in the textile industry. This flagship project perfectly aligns with our CPI Roadmap. However, there are additional challenges in this industry that we aim to address through further collaboration. Read our latest articles or connect with us on LinkedIn to learn more about the TEXPOWER project and our work in the textile industry.
You might also be interested in
Acknowledgement & partners
This project is co-funded with subsidy from the Dutch Enterprise Agency and the Ministry of Economic Affairs within the context of the Circular Plastics NL Growth Fund.
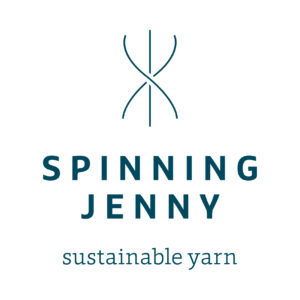
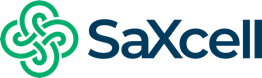

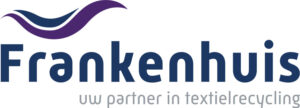
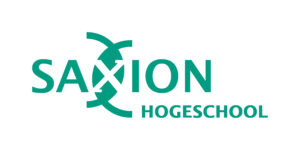
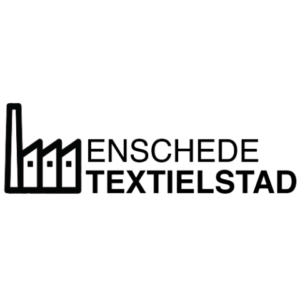
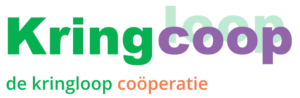