Spray drying is a very energy intensive process to dry milky products into functional powders. Considerable energy savings can be achieved if (more) water is removed prior to the spray drying operation and a more concentrated solution is atomized and dried. The EEMS project focused on reducing energy requirements in spray drying processes.
In short:
- Spray drying is used to dry milky products into functional powders
- Drying is a very energy intensive process using hot air
- Higher solids loading has the potential to save 20% energy
Incentive
Spray drying is a very energy intensive process to dry, amongst others, milk products into a functional powders. A liquid with typically 50% solids content (absolute level highly depending on composition) is atomized in a high pressure atomizer and dried under the influence of hot air. The internal liquid flow in a high pressure swirl nozzle largely influences the liquid sheet breakup and hence determines droplet size distribution, which in turn determines spray drying efficiency and product quality. High solid content liquids are typically highly viscous and depending on composition can exhibit non-Newtonian flow behavior.
Currently the level of understanding is not yet sufficient to allow for a higher solids loading, which has the potential to lead to a 20% energy reduction, because more of the liquid can be evaporated in the more efficient evaporator or by reconstituting at a higher solids content. The EEMS project aimed to develop fundamental understanding on the complex fluid dynamics inside the nozzle as well as the liquid sheet breakup, through high fidelity numerical simulations and non-invasive monitoring techniques.
Objective
Considerable energy savings can be achieved if (more) water is removed prior to the spray drying operation and a more concentrated solution is atomized and dried. The EEMS (Energy Efficient Milky Sprays) aimed to study the effect of solids content and main constituent components of model liquids on atomization efficiency of the nozzle. The research used a combined experimental and numerical approach to gain this understanding.
Ultimately this should lead to recommendations for design and operational principles to help meet the Dutch climate agreements to reduce greenhouse emissions by reducing the energy requirements of spray drying processes.
Results
First of all, binary droplet collisions were investigated using a Local Front Reconstruction Model (LFRM) and dedicated experiments for both Newtonian and non-Newtonian liquids. A parameter study showed that the collision outcomes are highly dependent on the power-law index, i.e. the boundaries of collision maps are not only dependent on the viscosity of the liquid but also on the power-law index.
Secondly, the primary break-up of laminar circular jet and rectangular jets was investigated both numerically and experimentally. LFRM was able to capture the break-up length, the droplet sizes, the axis-switching behaviour (for rectangular jets) and the complex interface deformations during the bursting of the jet in the second wind-induced regime. Based on the computational results of the circular jet in the second wind-induced regime and the rectangular jet, it is concluded that the outlet velocity profile of the nozzle largely influences the break-up length of the jet.
In addition, the novel Structured Laser Illumination Planar Imaging (SLIPI) technique was developed and used to determine the atomization of liquids experimentally for a Delevan SDX-III nozzle. Besides the size of the droplets, the velocity profiles outside the nozzle were studied for both water and more viscous fluids (using maltodextrin solutions). These measurements will be extended in the extension of the project and reported in the DRAGONS Egg project.
Follow-up project: DRAGONS Egg
Besides the studies outside the nozzle, the fluid flow inside the nozzle was also studied. To allow visualization of the flow and the air core inside the nozzle, the nozzle was scaled hydrodynamically to 5 and 10 times the initial size, respectively. Initial findings on these scaled nozzles indicate that the formation of the air core in the nozzle and its stability point are correlated with the inlet Reynolds number. These findings will also be explored further in the extension of the project and reported in the DRAGONS Egg project.
To study the flow inside the nozzle numerically, the contact angle near the gas-liquid-solid surface needs to be represented correctly. In this project, we developed a new approach for the implementation of the gas-liquid-solid contact points. The implemented contact angle model will be used in the extension of the project and in the DRAGONS Eggproject to simulate the flow inside the nozzle.
You might also be interested in
Articles / Publications
Acknowledgement & partners
This project is co-funded by TKI-E&I with the supplementary grant 'TKI- Toeslag' for Topconsortia for Knowledge and Innovation (TKI’s) of the Ministry of Economic Affairs and Climate Policy.
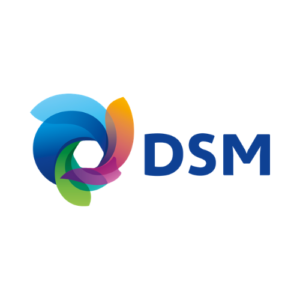
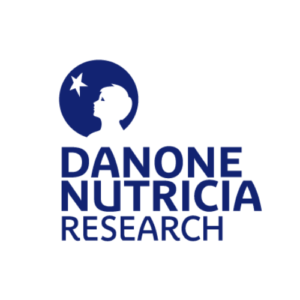
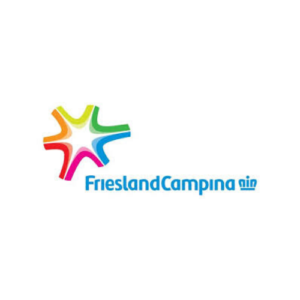
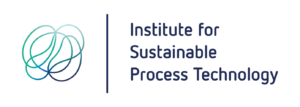
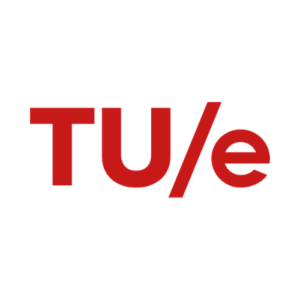