Within the process industry some 25% of the energy is used for separation processes. The main separation process used is distillation, which has a low efficiency. The goal of this project is to scale-up hybrid silica and polymer-based organic solvent nanofiltration membranes to 0.1 m2 of membrane area using low-cost, high-quality ceramic supports.
In this way, a breakthrough is obtained in stable low-cost organic solvent nanofiltration membranes and the position of the Dutch industry is maintained as playing a major role in production of these membranes.
Motivation
Within the process industry some 25% of the energy is used for (thermal) separation processes. The main separation process used is distillation, which has a low efficiency. It is well known that membrane processes are much more efficient than distillation. Molecular membrane based separation processes like nanofiltration are used more and more in the industry in combination with distillation or extraction as hybrid process solutions or even to replace them. Using these membranes in energy intensive processes will save significant amounts of energy.
Much organic solvent nanofiltration (OSNF) membrane R&D in the Netherlands is focused towards more fundamental development of membranes (TRL 2-4). Scaling-up of these and other membranes is still needed. With the developments at CoorsTek of low cost ceramic supports the opportunity to scale-up membranes, developed in previous projects, to a low cost solution for high demanding applications has arisen. In the case of OSNF the membrane costs in combination with stability and lifetime is a limiting factor that needs to be solved to come to implementation.
Goal
To scale-up hybrid silica and polymer based organic solvent nanofiltration membranes to 0.1 m2 of membrane area (move from TRL 4 to 6) using low cost, high quality ceramic supports. By this a breakthrough is obtained in stable low cost organic solvent nanofiltration membranes and the position of the Dutch industry in playing a major role in production of these membranes. This proposal is aimed at developing a 40% more efficient separation process via replacement of thermal separation by pressure driven separation processes. This by using low cost ceramic (hollow fibre and multi-channel) membrane supports and apply membranes via either sol-gel technology or coating of existing polymers to make membranes with tuned retention in OSNF and to prove the good and stable performance of these membranes in selected industrial mixtures. For efficient separation of the selected aromatic and aliphatic mixtures the membranes should have a solvent permeance of at least 1 l/m2hbar and a retention of 200 Dalton at temperatures up to 140°C. For the concentration and recovery of edible oils in the food industry a retention of 800 Dalton is sufficient.
You might also be interested in
Articles / Publications
Acknowledgement & partners
This project is co-funded with subsidy from the Topsector Energy by the Ministry of Economic Affairs and Climate Policy.
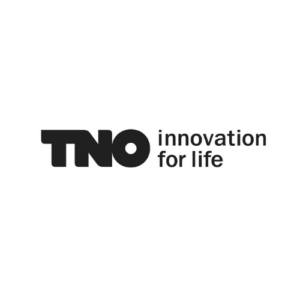
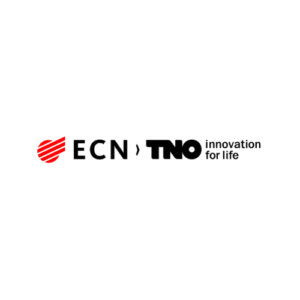
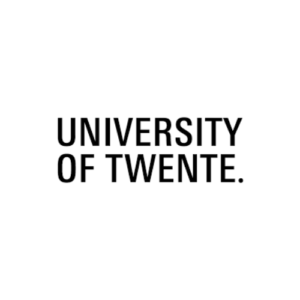
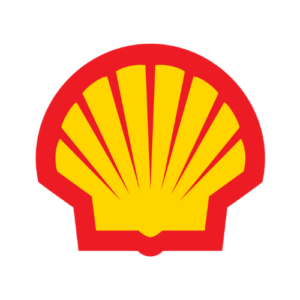
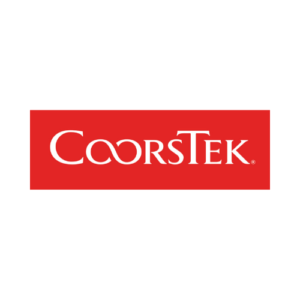