AMAZING project is about replacing large-scale high-temperature cracking processes with electrically driven thermocatalytic dehydrogenation of alkanes to alkenes.
In short:
- Amazing is a German-Dutch project that focused at producing sustainable building blocks for plastics manufacturing.
- The membrane material of choice was lanthanum tungstate (LWO), a mixed proton/electron conductor. Additionally, a model was developed to derive transport properties of these materials under reducing conditions.
- The technological feasibility of electrified crackers and electrified proton pump systems still needs to be confirmed.
- Results show that water splitting on the permeate side has a substantial impact on the apparent hydrogen permeation measured in conventional permeation experiments.
Achieving CO2 emissions targets through Innovative Green Chemistry
Satisfying the ever-increasing global demand for energy and materials, while achieving the ambitious CO2 emissions targets of the EU for 2030 on climate change, requires the utilization of renewable resources (e.g. wind, solar) in the fuels and chemical industries.
The German-Dutch AMAZING project has researched making the cracking processes employed to produce building blocks for plastics manufacturing more sustainable. By replacing large-scale high-temperature cracking processes (e.g., steam cracking of naphtha and/or ethane) driven by fossil-based fuels with renewable electricity to conduct thermocatalytic dehydrogenation of alkanes to chemical building blocks (alkenes), the CO2 emissions associated with energy-intensive cracking reactions can be reduced significantly.
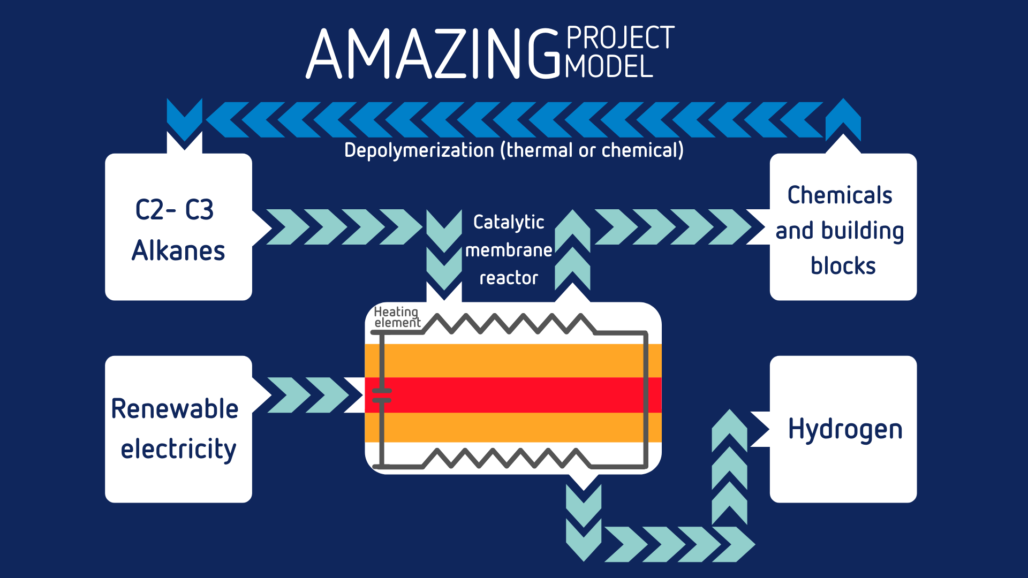
Advances in proton pump membranes, catalysis, and manufacturing
The goal of the AMAZING project was to develop proton conducting membranes to enhance the non-oxidative dehydrogenation of alkanes to alkenes, which are essential building blocks for the chemical industry. The AMAZING project consisted of a German and a Dutch part. The German part focused on the manufacturing of the membranes. The Dutch part focused on the fundamentals of proton transport through these materials, dehydrogenation catalysis, process design and technical evaluation and mechanical strength studies.
Technological and techno-economic feasability
The technological and techno-economic feasibility of catalytic membrane-assisted alkane dehydrogenation were investigated using reaction mechanism and process simulation studies. On the catalyst scale, the alkane dehydrogenation rate over a PtSn/ZnAl2O4 catalyst was inhibited by high olefin and high hydrogen concentrations, and by repulsive interactions between adsorbed species. Co-feeding steam enhanced product desorption and thereby increased reaction rates, but also structurally modified the Sn content. Pt is therefore preferred to PtSn as catalyst active phase in membrane reactors. On a process scale, MPEC membranes were unsuited for integration with high temperature alkane dehydrogenation, due to a restricted driving force for permeation.
Proton pump membranes: an attractive industrial alternative
On the contrary, the usage of proton pump membranes could be an attractive industrial alternative to traditional olefin production pathways, as its capital investment and energy input are 20-30% lower. Nevertheless, fully renewable electricity needs to be utilized to substantially reduce the carbon footprint. Moreover, electrifying conventional alkane cracking technologies could potentially lead to a similar improvement in carbon footprint as industrial implementation of proton pump membranes. However, it should be noted that the technological feasibility of electrified crackers and electrified proton pump systems still needs to be confirmed.
Manufacturing process from a mechanical point of view
The manufacturing process of the green hydrogen-generating ceramic membranes was studied from a mechanical point of view. Making these membranes is a challenge, since they are made of new chemical compositions, and they are not uniform, containing pores of different sizes and in different quantities. Due to these features, they often deform and crack during manufacturing. In this project, the manufacturing process was modeled via finite element methods. The virtual reconstruction of the process allowed access to information that is experimentally unavailable: the evolution of the membranes’ structure, porosity and internal stresses throughout their manufacturing. Strategies to minimize the manufacturing issues are then identified, both in terms of structure optimization and manufacturing processes. Additionally, an ultra-efficient numerical code is implemented, to enable the path towards a digital twin of the membranes’ manufacturing.
You might also be interested in
Acknowledgement & partners
This project is co-funded with subsidy from the Topsector Energy by the Ministry of Economic Affairs and Climate Policy.
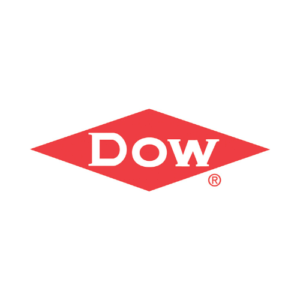
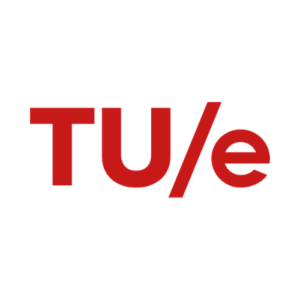
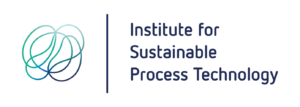
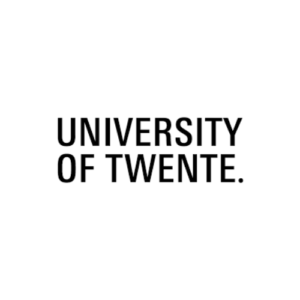
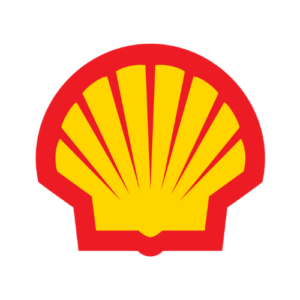