The recycling of PDM-waste is a tremendous challenge. After sorting, one of the streams you end up is the mixed plastics stream (DKR350) for which pyrolysis seemed to be a suitable processing technology. However, recent research conducted by the Circular Plastics Initiative (CPI) indicates that DKR350 as such it is not a feasible feedstock for pyrolysis. The pyrolysis product contains too many halogens and oxygen to serve as feedstock for new plastics.
“The solution lies in better plastic separation beforehand, post-treatment of the pyrolysis oil, or alternative processing through gasification. Ideally, the solution lies in design for recycling.” Ronald Korstanje and Sasha Kersten argue in this interview with NPT magazine.
Household plastics remain a challenge
The challenge of effectively recycling households plastics was recently taken on by the Circular Plastics Initiative (CPI). Together with plastic producers, product designers, plastic processors, waste collectors, waste sorters, process technologists, and polymer experts, they sought a suitable method for recycling PMD, which is the home sorted plastic, metal and drinkcarton waste from households .
Polyolefins are by far the most commonly used polymers for packaging plastics serving a wide range of products. From the plastic wrapping of our cucumbers, the bottles for our liquid detergend, or plastic films used to secure our packages. At its ‘end-of-life’, the PMD is collected and sorting facilities then separate different plastic fractions referred to as DKR310 (films) and DKR350 (mixed plastics).
Pyrolysis as a recycling method for DKR350
The CPI research focused on processing this DKR350 stream for pyrolysis and gasification. Here the plastic is rapidly heated to 500-550 or 800-1000 °C respectively, breaking down the polymer chains to oligomers and/or monomers. The result for pyrolysis is an oil-mixture composed of a variety of monomeric and oligomeric compounds, a wax and various halogens and oxygenates; for gasification a syngas with other monomeric compounds.
From these results, it turned out that the sorted DKR350 stream was not suitable for this type of pyrolysis. “We now for the first time have clear scientific and public results how a mixed plastic stream is processed during pyrolysis connecting all the steps in the chain. This learned us a lot and gave a lot of valuable new insights. We now have a better understanding of what still needs to be done to close the loop,” says Ronald Korstanje. These insights are important, Sascha Kersten and Ronald Korstanje agree.
“At the start of the project in May 2020, plastic recycling was still in its infancy. There was no cohesion within the chain: everyone had it’s own approach and actors were not familiar with each other’s technologies and knowledge position. They simply didn’t speak the same language.
That has all changed now: “There is now collaboration between different parties, creating a mutual understanding.” The CPI has played their role to bring these parties together and collaborate in a transparent and cooperative way; we see this is very important. “We have facilitated an industry-wide collaboration between different parties . As a result, people see opportunities to improve their own performance and new possibilities arise.”
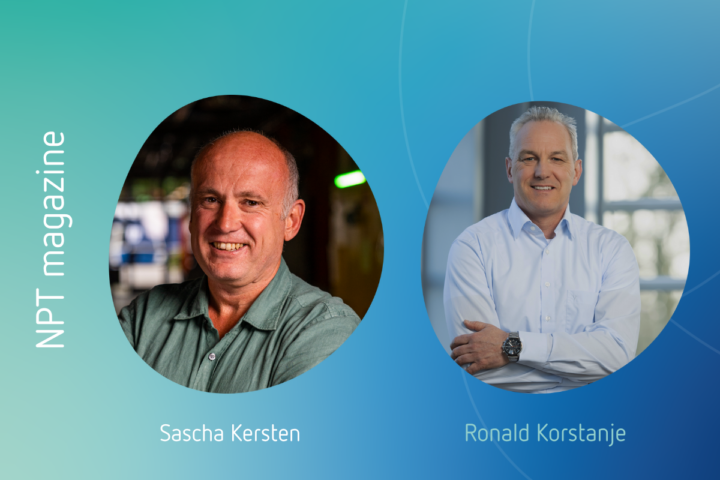
New game, new chances
Korstanje is optimistic that there will be further improvement, including finding an effective method for recycling DKR350. All participants in the project recognize the urgency, and almost all of them are collaborating on follow-up projects. New CPI projects related to pyrolysis have already been started up. Kersten even observes a change among plastic producers, who ideally prefer working with feedstock that has the same specifications as petroleum – a fantastic raw material with excellent specifications and consistent quality.
“If you take a close look at how PMD arrives at the waste collector and the mess that PMD plastic actually is, you realize how challenging it is,” says Kersten. He hopes and expects that major plastic producers will become more willing.” Of course, they will want to hold onto specifications derived from petroleum for as long as possible. But we see that they are realizing they need to approach things differently to successfully establish this recycling chain. And we are ready to support them with that”
For more information, visit the Circular Plastics Initiative (CPI) website.