At the Hydrohub MegaWatt Test Centre, located at Entrance at Hanze in Groningen, the first green hydrogen has been successfully produced under high pressure and at relatively high temperatures (up to 80 °C). This achievement marks a significant step forward in the development of more efficient and scalable electrolysis technologies.
First hydrogen produced
The Hydrohub MegaWatt Test Centre was established to test electrolysis at an industrial scale and to bring innovations from the lab to practice. The facility houses two types of electrolysers of up to 250 kilowatts: an alkaline electrolyser and a PEM (proton exchange membrane) electrolyser. Over the past years, a state-of-the-art facility has been developed that meets strict European industrial safety standards and offers extensive options for variable testing. The alkaline electrolyser has started up successfully and produced the first hydrogen. The PEM electrolyser is also expected to be commissioned within a few weeks. With the successful production of the first hydrogen, research can start.
Electrolysis is a process in which electricity splits water into hydrogen and oxygen. When powered by renewable energy such as solar or wind, the resulting hydrogen is classified as ‘green hydrogen’. The chemical industry sees green hydrogen as an important raw material for producing sustainable products and significantly reducing CO₂ emissions. An important condition is that the price of green hydrogen must become cost-competitive with hydrogen produced from natural gas.
Electrolysis in practice
At the test centre, experiments are conducted using large-scale equipment under varying conditions, such as fluctuating power input, elevated temperatures, and increased pressures. “Producing hydrogen at higher pressure and temperature can help reduce energy demand,” says Andreas ten Cate, Program Director at ISPT.
Higher temperatures increase the efficiency of the electrolysis process. Additionally, elevated pressure reduces the need for compression when transporting hydrogen to end-users. This can result in significant energy savings in an industrial setting. Finding the optimal balance between pressure, temperature, and efficiency – while maintaining flexible operation – depends on the system and remains an open question. The test centre is carrying out further research into this.
I am proud that through our co-funding we were able to contribute to the realisation of this important facility. This will undoubtedly accelerate the development of robust, large-scale electrolysers.
Rob Kreiter, Director of TKI Energy & Industry
Innovation and collaboration throughout the hydrogen value chain
The test center will be ready within a few weeks to start conducting research with the two electrolysers. The PEM electrolyser, developed by TNO, has a flexible Balance-of-Plant and is ideally suited for testing new components. It forms a vital link between the research conducted in the Faraday Lab and industrial application.
The alkaline electrolyser is more like a standard industrial installation. It will not only serve research purposes but will also be used for training and education.
Both systems are installed at Entrance – Hanze’s Centre of Expertise Energy. Entrance provides the infrastructure and supplies personnel for the daily operations. The test centre is now open to new partners and companies that want to contribute to the hydrogen transition.
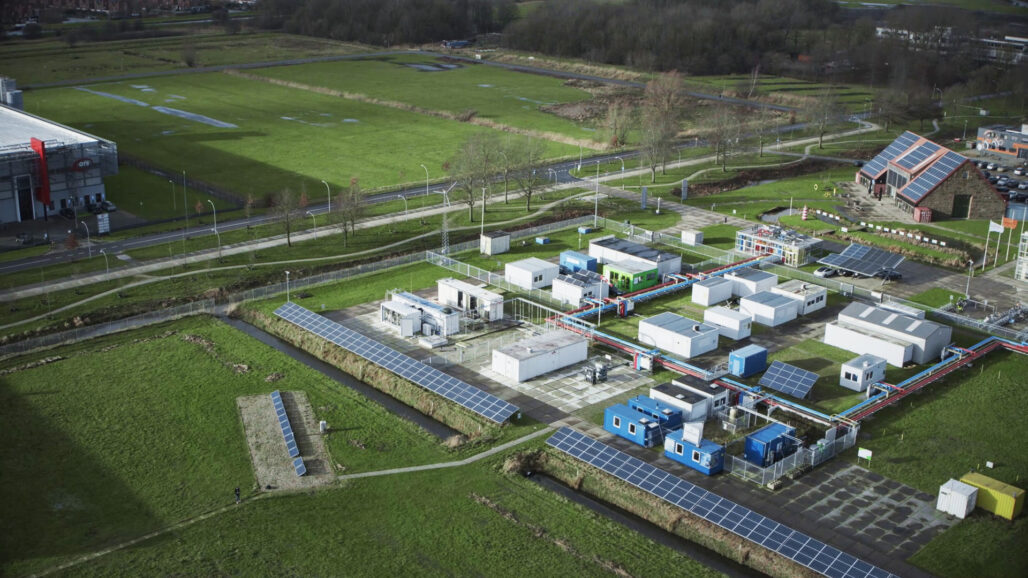
The MegaWatt Test Centre is a collaboration between Shell, Nobian, HyCC, Yokogawa, Yara and Groningen Seaports, and the knowledge institutions Entrance (Hanze), TNO, University of Groningen, and the Institute for Sustainable Process Technology (ISPT). The development was partly supported by the TKI Energy & Industry, the Ministry of Economic Affairs and Climate, and the Province of Groningen.
More information
ISPT:
Carol Xiao
carol.xiao@ispt.eu
+31 6 2849 4183
Entrance:
Marcel Koenis
m.j.m.koenis@pl.hanze.nl
+31 6 18684798
TNO:
Tara Abkoude
tara.vanabkoude@tno.nl
+31 (0)61 780 96 45
Acknowledgement
Dit project is medegefinancierd door TKI-Energie uit de Toeslag voor Topconsortia voor Kennis en Innovatie (TKI’s) van het ministerie van Economische Zaken en Klimaat