The FLEXSTEAM project aims to improve the way we can store and re-use thermal energy by using so called ‘Phase Changing Materials’ (PCMs).
To achieve a fully circular economy we will have to be able to close our material but also our energy loops. Re-using, storing and upgrading energy is an essential part of creating a sustainable system. In the industry a large part of the energy usage comes in the form of heat.
Heat buffering is very important for the integration of heat pumps in existing industrial processes. By focusing on the efficiency of processes as well as replacing fossil resources with renewable ones we will be able to greatly reduce the industrial sectors’ dependence on fossil energy.
About the FLEXSTEAM project
A challenge lies in the storage of energy when the availability of sustainable resources to run for example the heat-pumps varies. Storing energy is in fact one of the biggest challenges we face in the energy transition because of the varying availability of renewable resources. Electrical storage is very expensive whereas thermal storage can be achieved relatively cheap by using so called ‘Phase Changing Materials’ or PCM’s. Often a composition of salts or organic materials, PCM’s change from solid to liquid and in the process store latent heat. This way they can store a lot of heat in a small amount of volume.
Steam storing
The technology developed will be used for the recovery and re-use of industrial leftover (waste) heat, directly as well as indirectly through the use of heat pumps. Apart from that it will also be able to increase the implementation rates of sustainable heat sources like geothermal and solar energy to generate process heat. Both can be used more effectively and efficiently if a thermal energy storage solution is present.
The FLEXSTEAM project is a joint exercise by TNO (project coordinator), ISPT, Royal Cosun, DOW, TataSteel B.V, Blue Terra and Bronswerk.
Progress and Results
Applications for thermal storage are identified within the processes at TataSteel and at DOW. At TataSteel the thermal storage is to be integrated in a waste heat recovery application, to generate steam. The storage system creates additional energy and cost savings by covering the mismatch between waste heat supply and steam demand. A dynamic simulation of the thermal storage system was done to calculate these annual savings, and will be used as a tool for further optimizing the sizing of the storage system.
At DOW the thermal storage is to be connected with the on-site CHP system, to enhance the flexible operation. The technical requirements for this thermal storage system are beyond the current possibilities of the PCM concept due to the higher temperature needed in this application. The study is focused on the general techno-economic feasibility of the thermal storage, when facilitating the flex-CHP operation in the 2030 energy system, with fluctuating prices for electricity and increased CO2 taxes.
The technical development in the project, addresses the characterization and selection of a suitable PCM, optimizing the thermal conductivity of the PCM, and the development of a modular solution for PCM elements that allow industrialized production on a larger scale. Adipic acid is selected as low cost thermal storage material. It shows a very stable performance during 98 cycles of repeated melting and solidification (Figure 1).
With its melting temperature of 150°C it can be used to store and generate steam at 3 bar. The thermal conductivity of adipic acid is enhanced by adding graphite to it. This allows to reach charging and discharging times in the range of one hour. The composite PCM is contained in sealed tubular elements. The thermal performance in terms of charge and discharge times of these elements is characterized in laboratory tests and can be adapted to the application requirements by selecting the diameter of the tubes.
The design of the laboratory prototype system is based on a conventional shell & tube concept, where the tubes consist of the PCM filled elements, closely stacked together. The PCM thermal system will be thermally charged by applying steam to the outside of the tubes, heating them above the melting temperature. In discharge mode hot water is circulated along the tubes, which will transfer their heat to generate steam again. The prototype design is finished and construction has started.
Outlook
The first tests of the system will start in Q1-2021. Initial tests will be used to characterize the thermal performance in terms of storage capacity and heat transfer rates. Various operating conditions will be applied and results will be used to validate the thermal system model of the prototype system.
The test results and performance chart will also be used as input for calculating the techno-economic feasibility in the considered applications at Tatasteel and DOW. When successful results are obtained the next step is to develop a pilot project for on-site testing.
You might also be interested in
Acknowledgement & partners
This project is co-funded with subsidy from the Topsector Energy by the Ministry of Economic Affairs and Climate Policy.
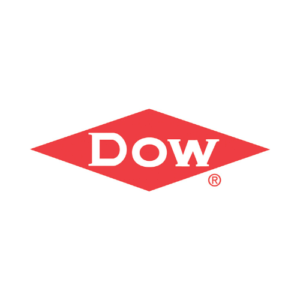
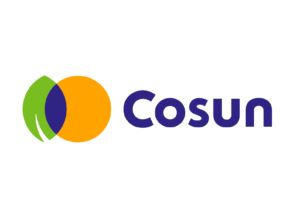
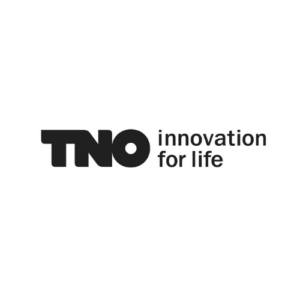
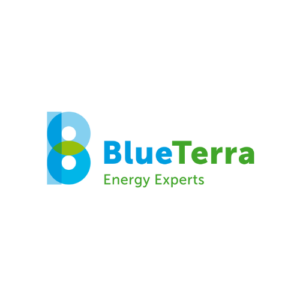
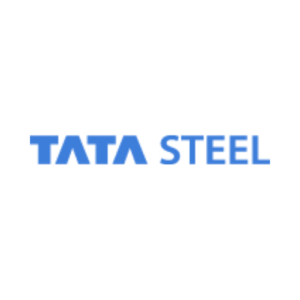
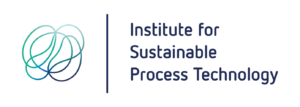
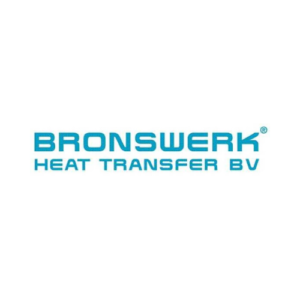