To further develop the compact electrically driven thermoacoustic heat (TA) pump technology and to prepare for technical demonstration on full scale.
The industry is a large consumer of energy and about two-thirds of the industry’s energy use is represented by heat. Often high-temperature heat is required, this heat is currently provided by burning natural gas. In order for the industry to meet the climate goals we will need to move to low carbon heating systems. One way to achieve this is by implementing high temperature heat pumps. These heat pumps, however, are not yet commercially available. The COMTA project proposes to start using the electrically driven thermoacoustic heat pump for industrial purposes. It can deliver heat of up to 200°C and it can cover a very wide range of temperatures with a fixed standardized design. Because this heat pump is electrically driven, it will become completely carbon free once fully renewable electricity supplies have become a reality in the future.
About the COMTA project
The overall project objective is to further develop the compact electrically driven thermoacoustic heat (TA) pump technology and to prepare for technical demonstration on full scale. This is achieved by experimental demonstration of a high COP1 over a very wide temperature interval from 100 to over 200°C using waste heat between 50-150°C under simulated and onsite test conditions (at DOW Terneuzen utility). A single full scale modular design will be realized that can serve a wide market including (petro)chemical industry, refining, paper & food industry. By its modular design steam production can be matched to the process in the range of 1 to 10 MW by installing one up to 8 units on the piston compressor. Energy is saved and a carbon free heat supply can be realized utilizing renewable electricity.
The project is coordinated by ECN.TNO. Other partners are ISPT, DOW, Bronswerk Heat Transfer and Howden Compressors B.V.
Aimed Results
The COMTA proposal serves as a last stop before full scale demonstration projects are initiated. The remaining R&D work serves to improve efficiency concerns optimizing membrane and heat exchangers. This is addressed by means of experimental component testing within the existing COMTA test set-up. Integration at the DOW steam utility and the onsite testing will verify the technical feasibility under operational conditions. Realization of the full scale design will be used for the verification of the techno-economic feasibility and to prepare for the full scale testing in demo projects.
This development results in net primary energy saving potential of 97 PJ per year and a CO2 emission reduction of 4.5 million tons/year within the sectors food, paper & board bulk chemical and refineries in the Netherlands. Major fuel cost savings for Dutch industry amounting to 4.8 billion Euro can be realized. In the future renewable electricity system carbon free electricity would result in even higher CO2 emission of 9.4 million tons/year. The worldwide market value for high temperature (steam) TA heat pump equipment and installation is estimated at 227 million euro per year during 20 years.
Status November 2020
Major developments in COMTA are the utilisation of an industrial piston compressor as driver and the strongly reduced dimensions of the pressure vessel (no resonator has been applied). Both developments will reduce future investment costs of the heat pump.
- The COMTA heat pump set-up is commissioned in March 2020 and first successful tests series have been executed including recent tests with saturated steam delivery at 168 °C.
- The saturated steam is pumped from source heat delivered by an oil circuit at 94 °C. The compressor ran at 1055 rpm and a dynamic pressure amplitude of almost 2.9 bars is obtained with a static pressure of 29 bars.
- The internal COP in the thermoacoustic core amounts to 41% of the Carnot efficiency. This number however excludes a high temperature loss in the heat exchangers and mechanical losses in the compressor.
Outlook
The thermoacoustic heat pump part originates from a previous test setup (TASTE) and this part will be optimised for the COMTA conditions (lower drive frequency). A large increase of thermal output is expected by an increase of the working pressure, optimised heat exchangers and a new regenerator suitable for the lower frequency. In this case even higher steam delivery temperatures up to 200 °C will become feasible. Measurement of the mechanical power delivery by the piston will give insight in system losses and guidance for further improvements.
You might also be interested in
Acknowledgement & partners
This project is co-funded with subsidy from the Topsector Energy by the Ministry of Economic Affairs and Climate Policy.
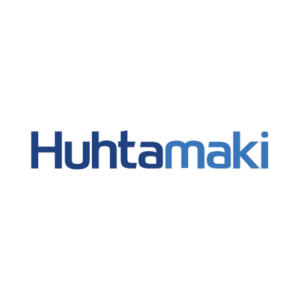
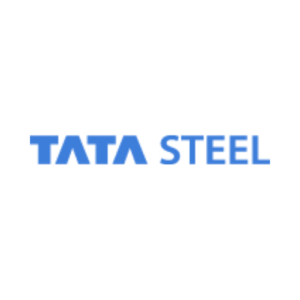
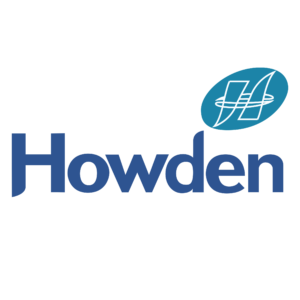
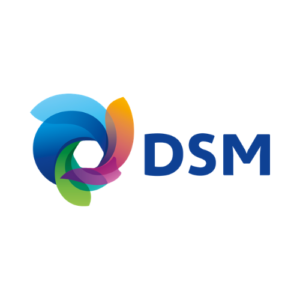
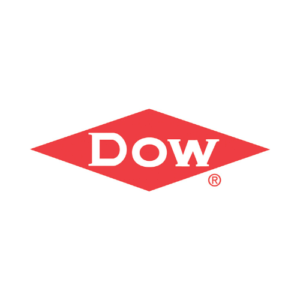
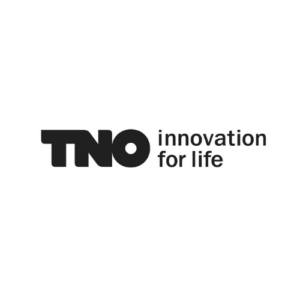
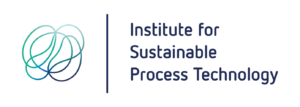
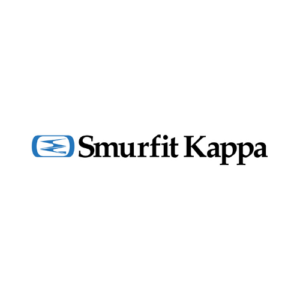
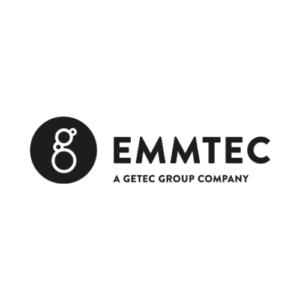
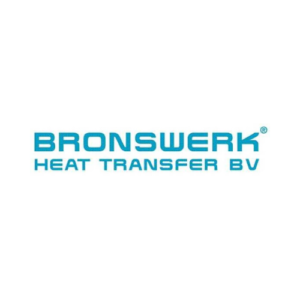