We are excited to present the advancements and outcomes of the COMPACT: Pulsed Compression II project, which focused on revolutionizing ethylene production through innovative pulsed compression technology. This technology capitalizes on the conversion of methane into ethylene, addressing the growing demand for cleaner carbon sources and reduced CO2 emissions.
In short:
- The project researches ethylene production by compressive activation of methane
- The goal was to explore the feasibility of this groundbreaking approach for industrial application
- The results suggest promising prospects for the application of this technology in ethylene production
Motivation
With increasing emphasis on sustainable practices, the COMPACT project sought to create a paradigm shift in ethylene production. Traditional methods relying on large-scale reactors and resource-intensive processes have prompted the need for a more energy-efficient and localized alternative. The pulsed compression technology, by utilizing nearly adiabatic compression, minimizes energy consumption and emissions while achieving the high temperatures required for methane cracking. Furthermore, the utilization of natural gas as a feedstock, as opposed to naphtha, contributes to emission reduction. This innovation also generates hydrogen, offering additional value, and holds promise for on-site liquid fuel production near remote gas fields.
Approach
The project delved into the intricate chemistry of methane cracking within a specially designed single-shot reactor (SSR). This reactor’s unique configuration allowed for a singular compression-expansion cycle, exposing the gas to extreme conditions with temperatures ranging from 800 to ~1800 K and pressures from 50 to ~700 bar. Through exhaustive research, optimal operating conditions were identified, paving the way for the development of a scalable continuous reactor design suitable for industrial application.
Principle
The core principle of the pulsed compression reactor (PCR) involves initiating a compression cycle through the controlled release of pressurized nitrogen beneath a piston. This rapid compression results in a swift rise in temperature and pressure within the reactant chamber, facilitating the conversion of methane to ethane and ethylene. However, the piston’s subsequent descent causes rapid quenching of the reaction mixture (up to 107 K/s), effectively ‘freezing’ the products and preventing further decomposition into carbon soot.
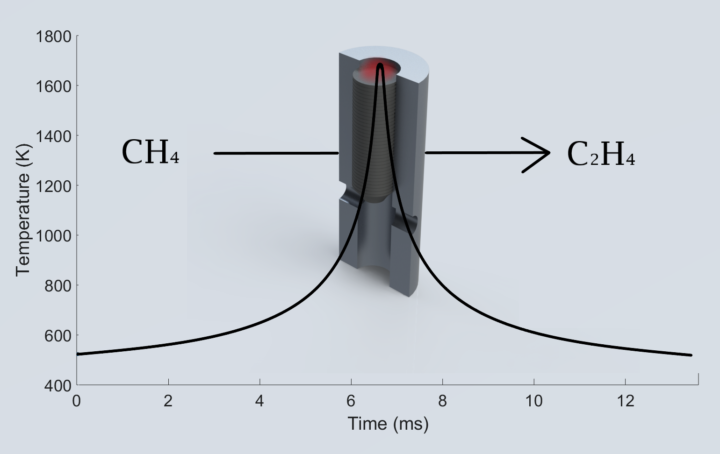
Objectives and Achievements
The project’s objectives were achieved through a carefully planned sequence of activities:
- Optimization of operational conditions: Through experimentation with CH4/H2 mixtures, optimal conditions were determined for maximal mass balance closure, precision, and accuracy.
- Continuous reactor development: A lab-scale continuous reactor was successfully designed, constructed, commissioned, and operated. This achievement marked a significant step toward practical application.
- Product conversion and selectivity: Experiments confirmed the conversion of methane to ethylene without the presence of oxygen, achieving remarkable selectivity at high-pressure conditions.
- Single pulse compression ratio: The attained single pulse compression ratio of 130+ stood as a testament to the unique capabilities of the pulsed compression approach.
- Yield maximization: Thorough optimization efforts resulted in an impressive 28% conversion rate, with a selectivity of nearly 99% for ethylene and other valuable products.
- Continuous operation: The continuous reactor demonstrated successful operation at 280°C, contributing to an elevated technology readiness level (TRL) of 6.
Future directions
While the accomplishments of the COMPACT project are commendable, further steps are envisaged to fully harness the technology’s potential:
- Enhanced initial gas temperature: Research avenues include exploring new reactor materials or designs to increase the initial gas temperature, thereby unlocking higher product percentages.
- Product separation techniques: To address lower product percentages compared to conventional ethylene streams, focus should shift toward economically viable separation methods such as membranes and adsorption processes.
- Chemistry under continuous operation: The influence of continuous operation on the underlying chemistry remains an intriguing area for investigation.
- Alternative conversion routes: Investigating alternative candidates like ethane pyrolysis could uncover more viable and energy-efficient pathways for ethylene production.
Conclusion
The COMPACT: Pulsed Compression II project represents a significant advancement in ethylene production technology. Through successful demonstrations of methane-to-ethylene conversion using pulsed compression, this project opens doors to a potentially more energy-efficient and sustainable future for the chemical industry. The innovative reactor design, combined with the achieved high conversion rates and selectivity, suggests promising prospects for the application of this technology in ethylene production.
With ongoing research and development, further refinement of this approach for industrial implementation is within reach. This progress marks a notable step toward a cleaner and more localized chemical production landscape.
You might also be interested in
Articles / Publications
Acknowledgement & partners
This project is co-funded with subsidy from the Topsector Energy by the Ministry of Economic Affairs and Climate Policy.
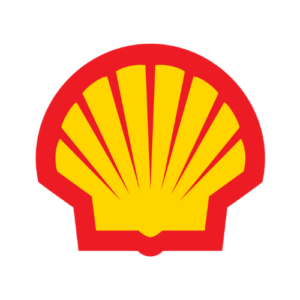
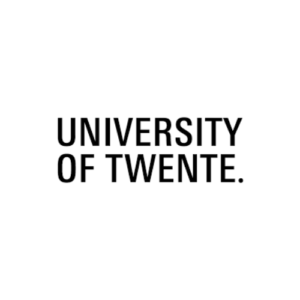
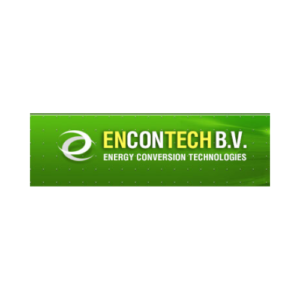
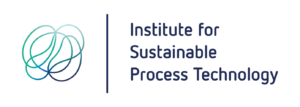
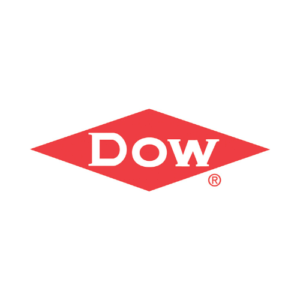