For each technology, safety is secured through permits, regulations, guidelines and standards. When it comes to the realization of large-scale electrolyzers for green hydrogen production, safety permits are currently lacking. That results in endless discussions and overdesign, which can slow things down tremendously. In this interview with magazine Petrochem, Carol Xiao and Hans van ‘t Noordende talk about ISPT’s new project on how the safety of electrolyzers can be tested and secured and what additional research is still needed for this purpose.
The European Green Deal envisions a CO2-neutral Europe in 2050. Large-scale green hydrogen production by water electrolysis plays a key role in realizing this goal. The Dutch targets for hydrogen in the Climate Agreement include an electrolysis capacity of 3 to 4 gigawatts by 2030. At the moment the largest existing hydrogen plant in Europe, only has a capacity of 10 megawatts. In less than 8 years, the plant’s capacity must therefore be massively scaled up.
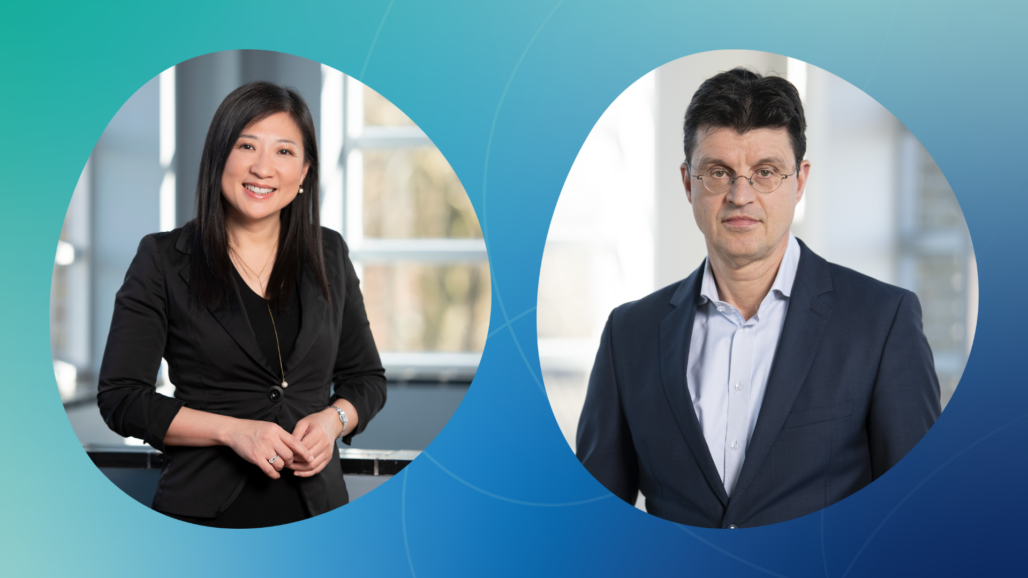
Safety for Green Hydrogen
Earlier this year, in January 2022, the Institute for Sustainable Process Technology presented the innovative design of a green hydrogen plant with a capacity of 1 GW, which could be operational by 2030. But not only scaling up the capacity and financing large electrolyzers are a challenge in reaching the climate goals. There is also a need for clarity on the safety of large scale electrolyzers. “Safety is currently the bottleneck for realizing electrolyzers on a large and small scale,” states Carol Xiao, our Program Manager for the Hydrohub Innovation Program in an interview with Petrochem. The question remains: how can we guarantee the safety of green hydrogen production in the future?
Bridging the knowledge gap
Hans van ‘t Noordende to Petrochem: “There are still many uncertainties in the area of security and safety. These are mainly concerned with the risk of the occurrence of explosions. At the current scale, these risks are so small that explosions almost never occur or have not yet occurred. As a result, there are very few historical incidents from which we can learn from. So we lack knowledge and experience and therefore don’t know exactly what can happen with large scale electrolyzers.”
Additionally, technology is changing. We are now using different materials, membranes and electrodes to make the process ever more efficient. We are moving toward flexible operations. Electrolyzers are going to run on green electricity, so they’re going to follow the wind and sun pattern. That also creates new conditions, where potentially an explosive mixture can derive. Even though, the industry has a lot of experience with hazardous substances and situations, this new situation asks for an extra level of carefulness. Therefore, we are considering the worst case scenarios, untill we can prove that the electrolyzers are completely safe.
Green Hydrogen Inherent Safety Practices on large industrial scale
The project Green Hydrogen Inherent Safety Practices was created for exactly that reason. In our project, developed with our partners, we aim to go from worst case scenario to credible scenario. The first objective of the project is therefore to establish assessment methodologies to assess risks of explosions with deflagration-detonation transition (DDT) and (delayed) ignition. We want to know what the impact and probability of explosions is. This project revolves on doing test and building data and models on top of that, and therefore deepen the understanding of the potential risks of explosions due to mixtures of hydrogen and oxygen in electrolysis equipment.
This article was previously published in online magazine Petrochem
Acknowledgement
This project is co-funded by TKI-E&I with the supplementary grant 'TKI- Toeslag' for Topconsortia for Knowledge and Innovation (TKI’s) of the Ministry of Economic Affairs and Climate Policy.