ISPT is proud to announce the release of our latest report “Enabling Safe Green Hydrogen Production on Industrial Scale – A Process Safety Study”. These outcomes mark a significant step forward in developing a safe green hydrogen value chain in support of Europe’s energy independency and climate goals.
Hydrogen as sustainable fuel and feedstock
As Europe transitions to a clean, secure, and self-generated energy system, renewable electricity — from wind, solar, nuclear and hydropower — will be the backbone of the energy mix. Hydrogen produced by electrolysis, will play a critical role as a sustainable fuel and feedstock across multiple sectors, helping to decarbonise heavy industry, transport and chemicals.
But scaling up green hydrogen production introduces complex challenges — especially in safety, integration and standardisation.
What’s in the report?
This report dives deeper into the technical safety risks, scenarios and design implications for electrolysis using Alkaline Water Electrolysis (AWE) and Proton Exchange Membrane (PEM) technologies. This report builds on our 2023 work on the Safety Aspects of Green Hydrogen Production on Industrial Scale.
Key findings include:
- Generic hazard scenarios and risk assessments
- Process safety management for electrolysers
- Effects of intermittent power supply on system degradation and safety
- Explosion and fire hazards specific to hydrogen and oxygen
- Review of Dutch ATEX guidelines (NPR7910-1) and their applicability to hydrogen
- Operational safeguards tailored to large-scale electrolysers
Our findings are supported by detailed bowtie analyses and hazop studies and can be applied across electrolyser technologies and system configurations — from gigawatt scale design.
The road to standardisation
Together with our partners, ISPT has initiated the development of a new NTA8221 process safety norm. These results will serve as essential input for the upcoming PGS40 Hydrogen Electrolyser guideline.
These actions form part of the activities within the Hydrohub Innovation Platform, aimed at accelerating safe and scalable hydrogen technologies.
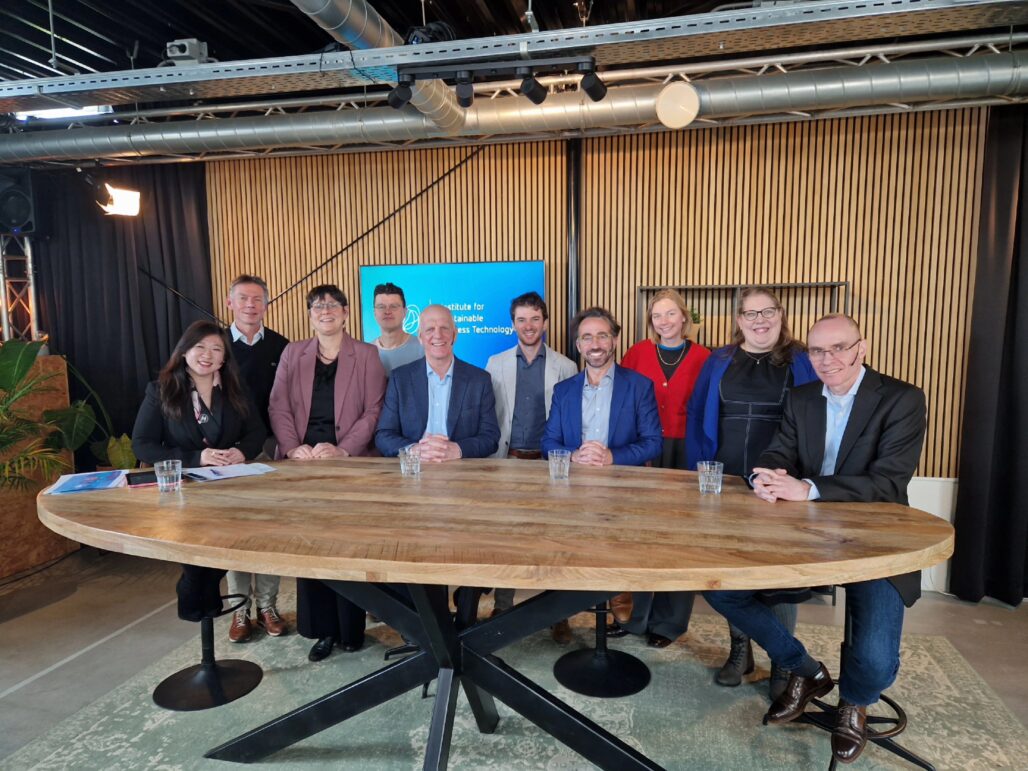
To complement the report, we have recorded an expert webinar to share key findings, practical examples and insights on next steps. Whether you’re a policymaker, technology provider, plant operator, or safety expert, the content provides actionable knowledge and inspiration.
Watch the webinar
Or watch the webinar on YouTube.
Q&A webinar
During our webinar, we received an overwhelming amount of questions in the chat. Our experts answered most of them on the spot. Questions that were still outstanding, are answered in the extensive Q&A below.
Q: Has there been any consensus on calculating leak sizes/ leak frequencies in hydrogen water electroysis?
A: No and wouldn’t expect industry-wide consensus since this will largely depend on specific type of electrolyzer technology, components and design / material selection
Q: Regarding ventilation of an electrolyser building, is there any standard that indicates the amount of air changes required to guarantee a good ventilation?
A: Usually we take the API for natural gas building facilities to estimate, but in Hydrogen don’t exist any standard. And because of that, we require to make CFD to see if there is a risk of stratification. I don’t have a generally applicable figure. For leaks within ATEX scope it might be possible to come up with such value. However, for incidents / loss of containment the ventilation rates required for preventing explosive mixtures depend on process pressure and general arrangement, so probably there’s no way to avoid CFD calculations. Another consideration is that equipment like separators may be located outdoors.
Q: In case of fire, is there a specific strategy for the firefighting?
A: Yes, there is. First, immediately stop the hydrogen supply and cool any equipment that may be exposed to the jet flame. Never attempt to extinguish a hydrogen jet flame with water, as the flame allows the hydrogen to burn off in a relatively controlled manner. If the jet flame is extinguished prematurely, it could lead to the formation of a larger gas cloud, which poses a much greater explosion risk if ignited. This scenario is significantly more dangerous than a controlled jet flame. Additionally, electrical components require special attention—power supply to affected systems should be shut off immediately.
Q: Is there consensus on vent design? CGA G5.5 versus EIGA 211/17 and thoughts on requirement to flare hydrogen with global warming potential.
A: Generally, design vents as safe location, i.e. assess all potential consequences for adjacent asset / people (in particular explosion overpressure / heat radiation from jet flame). Venting rates are expected to be very low and non-continuous. To be confirmed for respective H2 application. Flaring has disadvantages because of NOx emissions, sound and you need pilot gas (natural gas).
Q: What kind of software do you use to calculate effects of gas explosion?
A: Not just one software, depends on the scenario (congested / non-congested, etc.) and objectives. The different models have been described in detail in the first H2 safety report.
Q: How do you calculate distance between stacks/modules in a large-scale hydrogen production plant?
A: Accessibility (for maintenance, etc.) + risk of escalation depending on process pressure and realistic leak sizes which will determine length of potential jet flames and hence chance of a jet flame affecting nearby stack. Not purely a safety question but also economic risk: How much plot space would you sacrifice for safe distance preventing loss of additional equipment? Maybe also good to realize that potentially the inventory of a hydrogen pipeline with a loss of containment at the plant could be considered as the governing case.
Q: Is there any concern of authorities about venting H2, which has a GWP? Specially in The Netherlands or Germany?
A: Increased awareness but no indication yet that this would significantly affect the greenhouse gas avoidance potential of electrolyzers, work in progress …
Q: In case of H2 venting, is lightning protection strictly required whether an ATEX Zone 1 is determined?
A: Lightning Is not the only ignition phenomenon and lightning protecting would not necessarily prevent ignition. Therefore, vent should be designed and located such that the delayed ignition of the vent plume is safe.
Q: Could you give more information about membrane monitoring?
Membrane inspection is only possible destructively. Many causes and mechanism can play a role with membrane life time. Membrane life health condition monitoring apart from electrode aging and degradation is difficult to do although stack or cell voltage increase and gas crossover may be indicative.
Q: Which technologies have the option of cell voltage measurements?
A: Different water electrolysis technologies incl PEM and AWE are possible, solutions and vendors are available.
Q: What happens with the degraded membranes when they reach their end of life, what kind of waste do these generate and how it can be treated? Are there any other end of lifetime challenges?
A: This depends on the technology. Research is on-going on non-fluorinated membranes as well as on non-noble materials.
Q: Do you need a SIL3 PLC for the Safety System or is it a lower SIL level?
A: This depends on the design specific HAZOP / LOPA. A safety integrity system (SIS) is indeed practice.
Q: What is a reasonable stack hole size assumption to inform process safety time calculations for gas analyser effectiveness review?
A: The response time of a gas analyser can indeed be too slow in case of a certain instant failure scenarios. Whether this include failures with punctures and ruptures on cell or stack level is difficult to say since it depends on technology, design, materials, operating conditions etc.
Q: The membrane factor in the stacks is not there in hydrocarbon industry. Initiating event frequency of membranes failure is an unknown territory at this moment. Any data available for that?
A: There is no failure data available to our knowledge. The question is also whether this would be possible given the variety of technologies, see above.
This project was made possible in close collaboration with our partners: Shell, Yara, VoltH2, Ørsted, HyCC, Equinor, RWE, Plug Power, John Cockerill, Green Hydrogen Systems, Battolyser Systems, Royal HaskoningDHV, NEN and TNO. Thank you for your continued dedication and contributions to building a safer, cleaner energy future.
Acknowledgement
This project is co-funded by TKI-E&I with the supplementary grant 'TKI- Toeslag' for Topconsortia for Knowledge and Innovation (TKI’s) of the Ministry of Economic Affairs and Climate Policy.