Centrifugal contactors, such as RPBs, could provide significant improvement of separation processes in the chemical industry. This technology seems potentially suitable for replacing or debottlenecking current unit operations which suffer from mass or heat transfer limitations.
Incentive
Fast-changing consumer demands, changing environmental regulations and fluctuating raw material compositions are challenges for chemical production. A promising concept to meet these requirements is the development of flexible and mobile production equipment such as rotating packed beds.
The ImPaCCt (Improved Process Performance by Process Intensification in Centrifugal Contactors) project aimed at evaluating and quantifying the potential of rotating packed beds, leading to proper scale-up rules which were not available at the start of the project. The project was the continuation of the HiGee project finalized in 2015.
The RPB principle
Rotating packed beds offer the possibility to expand the operating window of common separation equipment due to the rotational speed as an additional degree of freedom. By applying the centrifugal field they provide intense contact between two or more phases and lead to excellent mass transfer rates and high capacities. A general setup consists of a vertical or horizontal aligned torus-shaped packing area and a motor to accelerate the packing to a certain rotational speed. Different rotational speeds lead to different mass transfer behavior. The operating mode can be co- or counter-current. Various types of packings and internals enable a flexible use or a tailor-made setup.
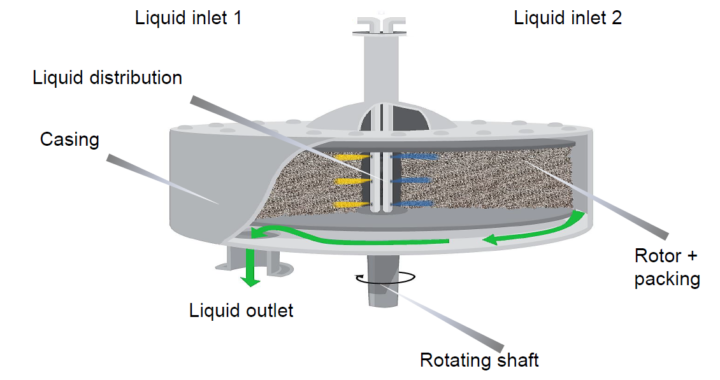
Activities
The overall project objective was to prove, how the RPB technology can facilitate the transition towards the next generation of smart, flexible, continuous production plants, with superior yield, purity and quality of products and improved productivity.
In the course of the project, the focus was set on the systematic characterization of rotating packed beds, the equipment improvement, and industrial case studies. Case studies from the fields of distillation, stripping, and liquid-liquid mixing were investigated. When the case studies proved their feasibility, the technology was further developed from the lab- to the pilot-scale in terms of radial packing length or throughput.
Results
In order to facilitate the implementation of RPB technology for the industrial application, the final report informs about design guidelines for liquid-liquid, gas-liquid and vapour-liquid systems. The guidelines are divided into operational parameters (e.g. flow rates, rotational speed) and design parameters (e.g. packing type, packing dimensions). An overview of the investigated parameter ranges and their influence on the RPB performance is given. The design guidelines are the summary of the achieved results throughout the project. They are an ideal basis to plan future investigations and evaluate new project ideas.
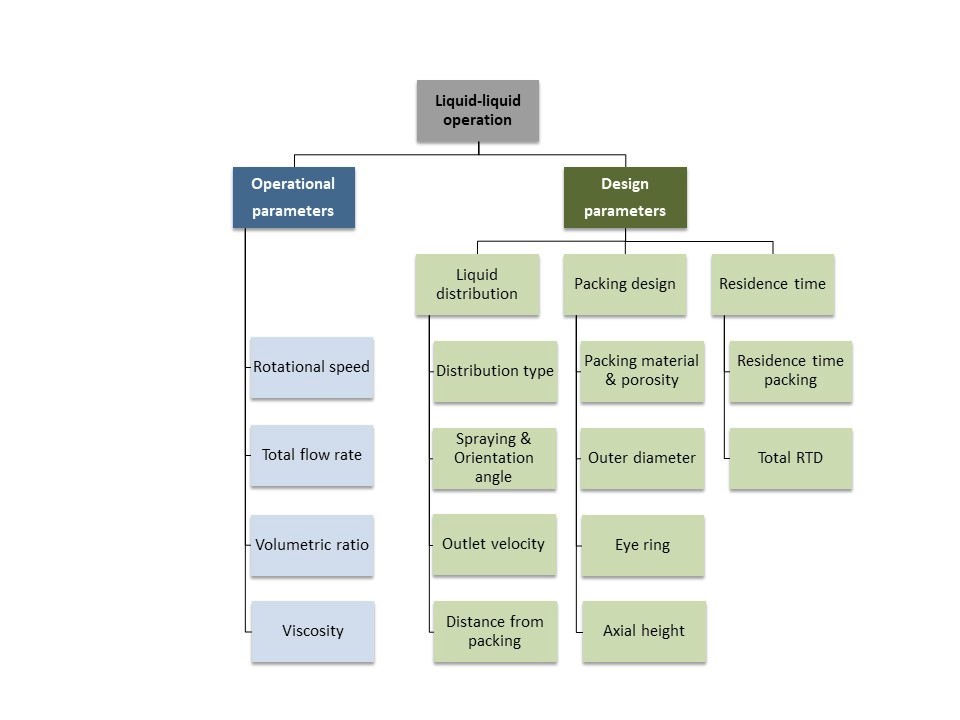
You might also be interested in
Acknowledgement & partners
This project is co-funded by TKI-Energy with the supplementary grant 'TKI- Toeslag' for Topconsortia for Knowledge and Innovation (TKI’s) of the Ministry of Economic Affairs and Climate Policy.
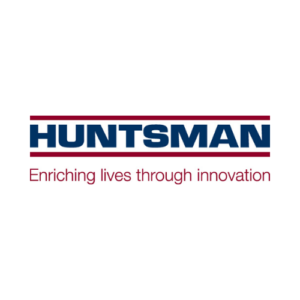
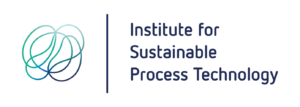
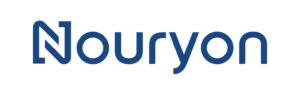
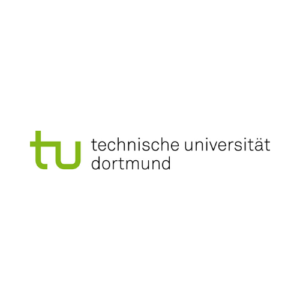
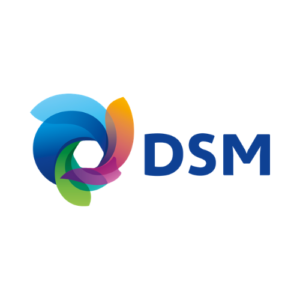