Traditional carbon-intensive blast furnaces are a major source of greenhouse gas emissions. In response, Tata Steel in the Netherlands is transitioning to more sustainable gas-based direct reduction (DRI) processes using hydrogen, which promises substantial reductions in carbon emissions.
In short:
- The GAMBA project seeks to reduce the carbon footprint of the iron and steel industry by transitioning from natural gas to hydrogen-based direct reduction (DRI) processes.
- A central goal is to develop and validate particle models for iron oxide reduction and iron carburization.
- These models will be integrated into reactor models to simulate and design sustainable industrial ironmaking processes.
- The project combines high-throughput experimentation and industrial evaluation to drive innovation in carbon-efficient steel production.
Tackling challenges in hydrogen-based DRI
Methane-based DRI technology is already commercially available and widely used. In a traditional DRI plant, iron ore is reduced primarily using natural gas, which consists mostly of methane (CH4). While this process emits less CO2 compared to coal-based blast furnaces, it still produces carbon emissions because methane contains carbon. The ultimate goal for Tata Steel in IJmuiden is to transition to a DRI process that runs 100% on hydrogen, eliminating carbon emissions altogether.
However, running a DRI plant entirely on hydrogen is not yet realized on an industrial scale, and there are several challenges to overcome. One critical issue is that DRI produced with hydrogen contains very little carbon, which can cause complications in later steelmaking processes that rely on a specific level of carbon. Therefore, improving our fundamental understanding of the carburizing mechanisms in DRI and identifying the limiting factors are essential steps in this transition.
A well-validated model developed through the GAMBA project will be instrumental in addressing these challenges by:
- Reducing energy consumption during the reduction process.
- Enabling the gradual shift from methane-based to hydrogen-based feedstocks.
- Optimizing the Fe-C quality of DRI for downstream processing, ensuring that operational challenges are minimized while using minimal carbon-based gases.
By tackling these technical barriers, GAMBA will significantly contribute to the industry’s decarbonization efforts, driving innovation in the steel production process while supporting the shift towards sustainable hydrogen-based technologies.
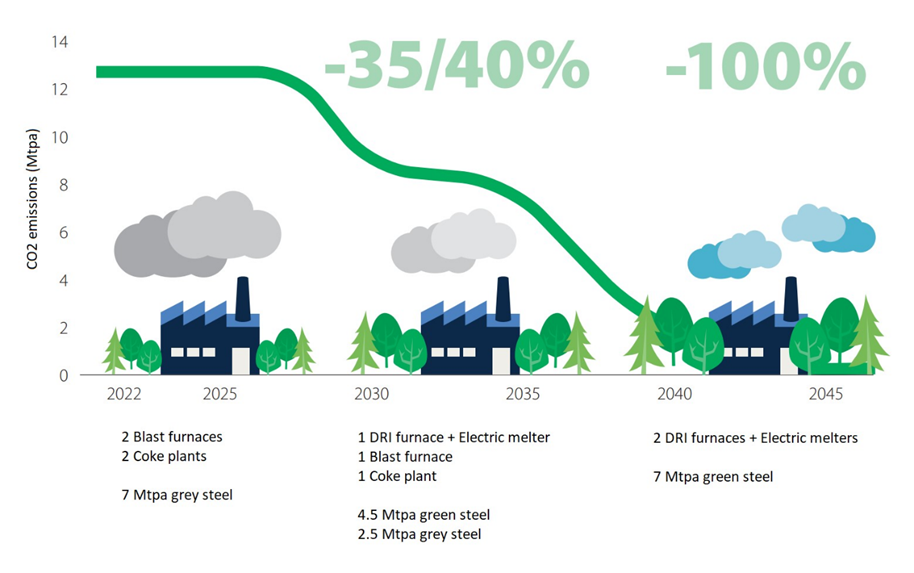
Our key activities
The GAMBA project aims to develop experimentally validated particle models for the reduction of iron oxide and iron carburization, which will be integrated into reactor models for the in-silico design of direct reduction iron (DRI) reactors. The University of Twente will lead the development of these models, simulating different gas scenarios, including hydrogen, methane, and synthesis gas. Tata Steel and the University of Twente will couple the particle models with reactor models to design efficient DRI reactors. High-throughput experimentation, conducted by both partners and DOPS, will validate the models through experiments at single particle and moving bed scales. This combination of modeling and experimentation will enable the project to evaluate industrial-scale scenarios, ultimately driving innovation and sustainability in the iron and steel industry.
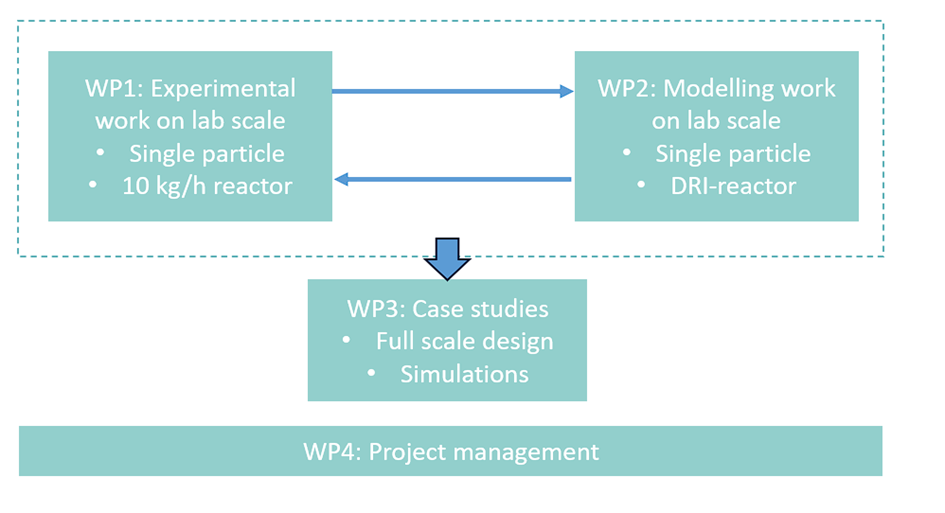
Expected results
By the end of the project, we will deliver:
- Data sets: Compilation of data from single particle and reactor experiments for model parameterization and validation.
- Validated models: Development of validated single particle models applicable for iron oxide reduction and potentially relevant for Fischer-Tropsch catalyst chemistry.
- Industrial evaluations: Evaluation of several industrially relevant cases to inform future developments.
Join the movement
Interested in being part of this transformative project? Join our community on LinkedIn or explore more insights through our newsletter. Together, we can accelerate the transition to a sustainable steel industry.
You might also be interested in
Acknowledgement & partners
This project is co-funded with subsidy from the Topsector Energy by the Ministry of Economic Affairs and Climate Policy.
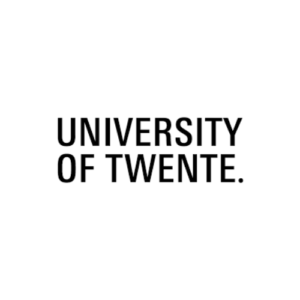
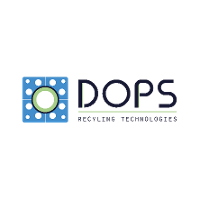
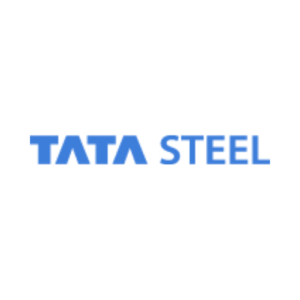