As the world moves toward net-zero carbon goals, the demand for sustainable materials is rapidly increasing. Plastics, essential in countless applications, must evolve to meet the demands of a circular, low-emission future. The Circular Aromatics Project, led by BioBTX B.V., is pioneering this transformation by converting mixed plastic and biomass waste—streams that are currently hard to recycle—into valuable chemical building blocks for plastics.
In short:
- Lab to Pilot Scale: Scaling the ICCP technology from TRL 3 to TRL 6, proving feasibility at pilot level.
- From Waste to BTX: Producing BTX from mixed plastic and biomass waste streams that are usually incinerated or landfilled.
- Towards Circular Plastics: Using refined aromatics to produce high-quality aramids, closing the loop in the plastics value chain.
Why is this project relevant
Today’s plastic waste streams are complex: often mixed, contaminated, and difficult to recycle. As a result, the majority are incinerated, contributing to emissions and resource loss. Mechanical recycling can’t handle these materials effectively.
Using BioBTX’s breakthrough Integrated Cascading Catalytic Pyrolysis (ICCP) technology, the project demonstrates how mixed waste can be efficiently converted into benzene, toluene, and xylene (BTX)—critical components in plastic production. This innovation supports the transition to a renewable, circular chemical industry, starting in the Netherlands, with global implications.
Activities in the Circular Aromatics project
To bring this innovation to life, the project will carry out the following key activities:
- Identify and characterize suitable plastic and biomass waste fractions for upcycling.
- Develop a scalable feedstock mix for catalytic pyrolysis.
- Design a fluidized bed reactor for efficient depolymerization of complex waste streams.
- Develop and optimize catalysts to maximize BTX yield and purity.
- Produce raw BTX at pilot scale and refine it in a commercial setting.
- Convert refined xylene into aramids, creating a high-value, circular end-product.
Expected results
By the end of the project, the ICCP technology will be demonstrated at pilot scale, proving its ability to convert complex waste streams into valuable circular aromatics. The refined BTX will be used as feedstock for aramid production, showcasing how mixed plastic and biomass waste can fuel the next generation of sustainable, high-performance materials.
This project will set a new benchmark for waste valorization, combining innovation, circularity, and commercial readiness—laying the groundwork for global adoption.
You might also be interested in
Acknowledgement & partners
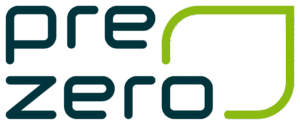
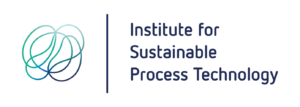
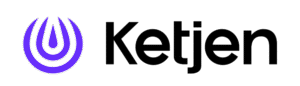
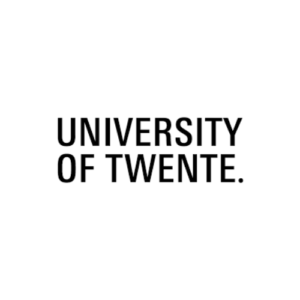
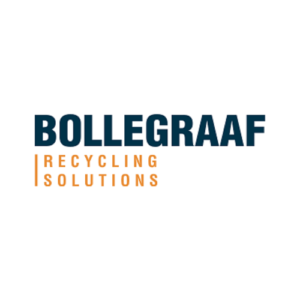
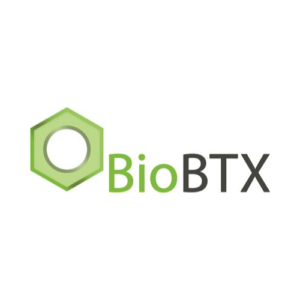
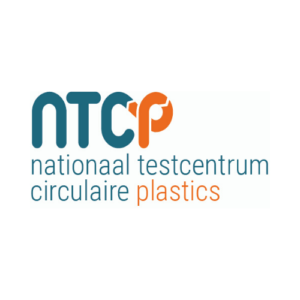
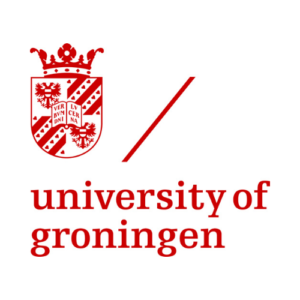
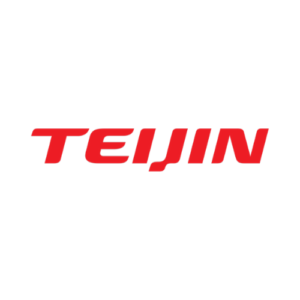
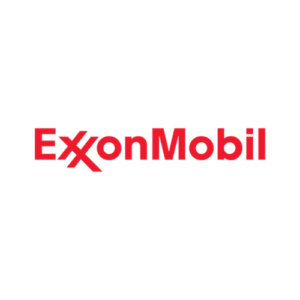