This is the second blog on how industry is establishing a sustainable future. The first blog introduced the role of industry in several themes which are currently most visible in the public debate around sustainability. This second blog is focused on one of those themes: green industry.
Negative emission
A production process with a negative emission: it sounds like an utopic concept, but it is reality – at least in the business of biobased plastics made from polylactic acid, also known as PLA plastics. Polylactic acid can be made with a NET, a negative emission technology, and it has many applications. As a NET product it is one of the steps towards a fully green industry, and it is a giant step. Especially combined with other sustainable innovations, like digitization and renewable energy.
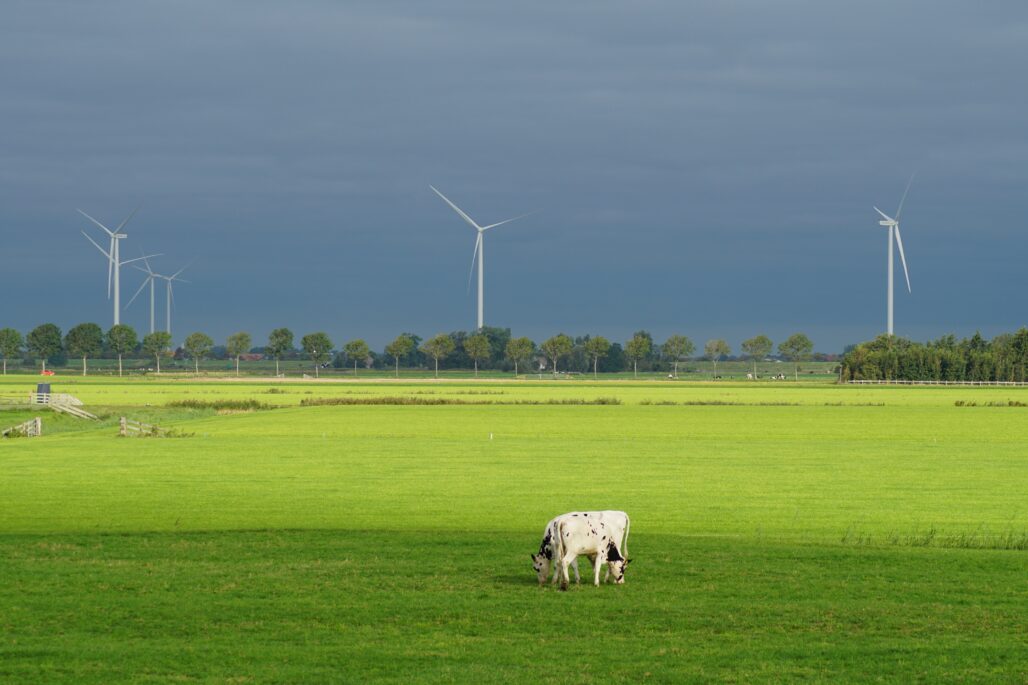
Various feedstocks
Global market leader in lactic acid and lactic acid derivatives is Corbion, formerly known as CSM: Centrale Suiker Maatschappij, or Central Sugar Company in English. Nowadays Corbion is a food & biochemicals company that, in a joint venture with the French company Total, produces sugar-based PLA plastics in its factory in Thailand. Biochemist Marcel Wubbolts, Chief Technology Officer at Corbion, explains the production process. ‘At the moment our main feedstock is cane sugar, one of the most important crops in Thailand, where the feedstock and transportation costs are low. We convert the cane sugar to lactic acid by fermentation. From that lactic acid, the joint venture makes lactide, which they then convert to PLA. The Thai factory is our first factory, if in time we would build a second factory, this could be located in another country. We might use another feedstock, more fitting with that factory’s surroundings. In Europe that would be wheat or corn – and sugar beets in the Netherlands and Germany. The feedstock depends on the location. We’ve also studied using second generation feedstocks, like sugar from corn leaves and stems instead of the grains, our fermentation processes are capable of processing those feedstocks and we have the ambition to switch to non-food feedstocks as soon as they are available. We don’t produce second generation sugars ourselves, so we depend on other industries, like the biofuel industry. At the moment the costs of those second generation feedstocks are still too high for industrial use, due to their lack of availability.’
Negative emission technologies
Wubbolts is passionate about developing sustainable solutions, and he elaborates on how polylactic acid contributes to a green industry. ‘We’ve done a life cycle assessment of lactic and polylactic acid production. And compared to, for instance, polystyrene – a plastic that can easily be replaced by (biobased) polylactic acid – PLA has a much better life cycle assessment. And secondly: because you use an agricultural product like sugar, which is basically CO2 stored by a green plant which has a negative CO2 score, and you combine this with the use of renewable energy, you can even achieve a negative emission. How? Well, our transportation costs are already low because we process our feedstocks locally, and the lactic acid fermentation process is extremely efficient. By combusting the bagasse – the waste materials of the cane sugar industry – we can generate thermic energy that can be used in the production process. If you do this conscientiously it will lead to a negative emission, which is why polylactic acid can become a NET-substitute for petro-based plastics, with comparable traits but bio-based, that can be either recycled or composted and is wholly sustainable. To achieve the goals of the Paris Agreement we also need to implement more of these negative emission technologies.’
Circularity and End of Life
Plastic waste, like plastic soup in the oceans, is one of the main concerns in the public sustainability debate. But its presence has more to do with human behavior than with the flaws of those plastics, according to ISPT director Tjeerd Jongsma. ‘If we throw them in the waste bin we can recycle this precious materials and return them to the chain,’ he says. Can PLA become a solution to the plastic waste in our environment? After all, PLA can be composted, which isn’t possible with petro-based plastics. Wubbolts doesn’t a priori recommend it though. ‘PLA doesn’t just go away that easily when you throw it on the compost heap. In contrast to petro-based plastics PLA disappears eventually, but it takes a long time. PLA can be composted under industrial conditions at a higher temperature of 65 degrees. We always recommend: re-use it as much as possible until the quality deteriorates and then you have to decide whether to recycle it chemically, or to compost it. Composting PLA will eventually turn it into CO2 again, which can be made into sugar by the green plant through photosynthesis. This also completes the circle. Both are valid solutions, but just like with normal plastics you have consider End of Life. Combusting it to generate energy is in itself not a bad End of Life. A bad End of Life is when it ends up in the oceans. Composting bioplastics is circular.’
Diverse applications
‘We’ve been working with lactic acid and lactic acid derivatives for eighty years, so we have a lot of experience with its applications, like for instance the bakery products, meat preservatives, cleaning and deliming agents we produce,’ Wubbolts continues, ‘but the speed of market absorption of PLA did surprise us a bit. Polylactic acid was really something new to us, but we’ve build a very diverse application range with it.’ Since the opening of their PLA factory in Thailand – which is fully operational but not producing at full capacity yet – in December last year Corbion has gained already at least 200 customers for PLA. ‘We are also active in biomedical applications of lactic acid, and produce other organic acids as well. We own a vinegar factory and we produce propionic acid, which like lactic acid also are preservatives. A recent acquisition is our algae business. Algae can grow on CO2and sunlight but we grow them on sugar to make oils and fats by fermentation. In the future we may even use CO2 as a feedstock directly, without photosynthesis by green plants.’
Sustainable innovations
ISPT’s Frans van den Akker describes digitization as ‘a quick win’, and just like at many other companies, it is a big theme for Corbion. Wubbolts: ‘Process data for instance, which we used to collect on different production sites. We’ve adapted the format of those data in a way that allows us to compare them better, which enables us to do big data analysis that will help us to become even more efficient.’ Electrification is another sustainable innovation that is high on the agenda, although Wubbolts considers this more of a long term investment. ‘We expect that electricity eventually will become cheaper and fossil based fuels will become more expensive, and then you have to make the switch. Together with ISPT we study the upcoming transition: what does the electrification of the biochemical industry entail, and how can we apply it within our company, maybe already right now, but very likely in the future.’
Wubbolts also mentions another important innovation, that can change the way we preserve sodas and fruit juices: PEF bottles. ‘Our company is divided in two main clusters. We have ingredient solutions, which contains our running business, like bakery ingredients, biochemicals and medical materials. The other business unit is innovation platforms, in which we study new growth markets for Corbion. And one of those platforms focuses on PEF, a polymer based on FDCA, which we make out of sugars. The PEF bottle has a lower gas-permeability than the PET bottle, thus allowing for a better preservation of the carbon dioxide in sodas, and a better preservation of e.g. vitamin C in fruit juice since it shields away oxygen. For the same reason, food that is preserved in PEF also is expected to have a longer shelf life than food preserved in PET, which can lead to less food waste. One of the UN development goals is SDG2, Zero Hunger, which we address with our preservation products and our packaging materials. What can we do to fight food waste? The other UN development goal that we have embraced is SDG12, Responsible Consumption and Production, which is closely related to the Circular Economy. How can we produce and consume in a more sustainable way?’
Time for change
Projects focused on sustainability and creating a circular system, are essential in forming the necessary momentum to create change. Furthermore, we need to increasingly underline what we need to do to establish a fully green industry: minimize waste and bring precious resources back into the chain. In addition, we need zero or negative emissions and we need industrial strategies that the old system lacks.
Want to learn more about industry’s efforts to establish a sustainable future? Read the first blog on the role of industry in the debate around sustainability here, and make sure to follow us on LinkedIn.