Liquid Gap Membrane Distillation combines leftover heat with box-shaped membranes
The development of a new separation technology by means of membranes – membrane distillation – started a few years ago and its effectiveness has been proven. Market introduction, however, is still limited by insufficient robustness of the technology as well as its cost price. The new Liquid Gap Membrane Distillation (LGMD) concept proposed in this new research can change all this. These new box-shaped membranes are stronger, cheaper and can operate at a lower temperature, making the re-use of leftover heat possible to operate the process. This means that the industrial energy consumption for process water preparation can be reduced. Not only will this contribute to making the industry more sustainable, it is also a very attractive prospect for the users to produce very pure water from their product (salt) waste streams that they can then re-use.
Limiting factors this project aims to overcome
Membrane Distillation is a very promising new technology, however it is not yet commercially viable. The main reasons for this are: mechanical/ technical (membrane breakdown, leakages); performance (flux and energy-efficiency); scalability (and thus high prices for the modules) and a lack of commercial-scale manufacturers. The aim of the LGMD project is to demonstrate that major steps forward can be made with respect to these limiting factors. The focus of the project will be on producing high-quality water, suitable as a boiler feed or demineralised water, from surface water as well as from salt industrial process waste-flows using the industry’s own residual heat to operate the process. This will make the energy input used to purify this water almost negligible as this heat would otherwise have to be cooled and discharged.
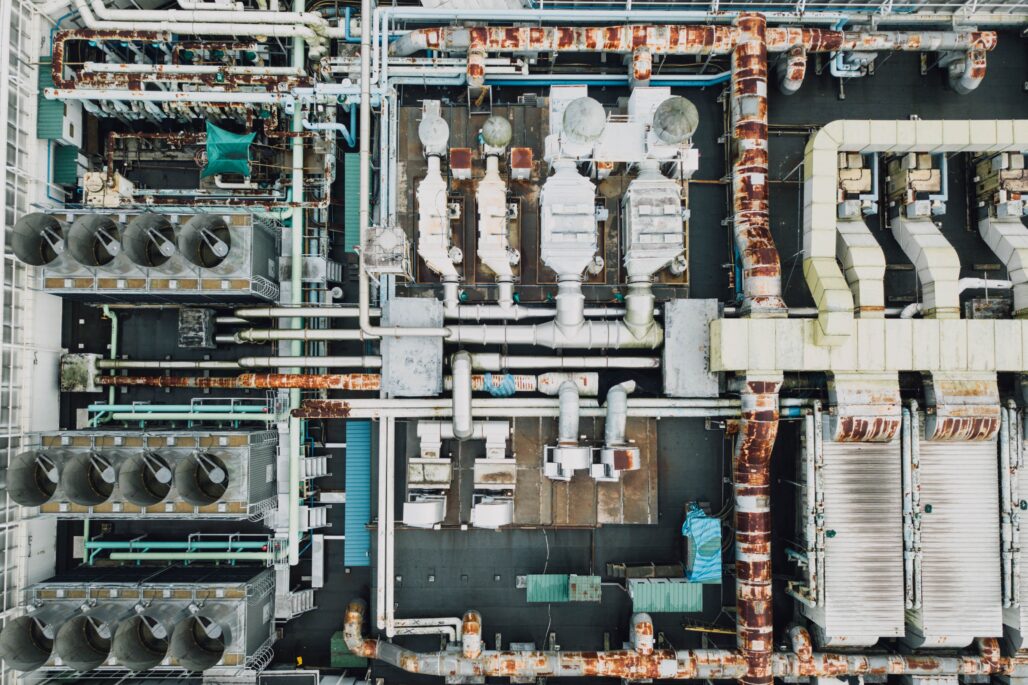
The Liquid Gap Membrane distillation module
For this purpose i3 Innovative Technologies B.V. will develop and test a new type of Liquid Gap Membrane Distillation (LGMD) module. The design of the module is derived from experience with small spiral-wound modules. With an improved membrane, different spacer configuration, changed flow channel dimensions, new heat-conducting materials and a new, potentially inexpensive construction method a big leap will be made in product, performance and price. WIC will evaluate the results for (and together with) the users Carbogen Amcis, Friesland Campina and Floating Farm as well as for the entire process industry. The results of this feasibility project will be shared through the networks of NL-Guts, ISPT, NMG and NWGD as well as by the three end users.
Possible savings and future perspective
The Dutch process industry uses around 600 million m3 of process water, in addition to this it also uses 10 times as much cooling water. Process water is made from soil, surface and drinking water and has to be purified to a very high quality. The reason for this is that our foods are prepared from this process water and therefore it has to last much longer than drinking water that has a shelf life of only two days. The energy consumption of drinking water preparation is approximately 1.5 kWh/m3 and bringing process water in the industry to the desired high quality costs even more energy. Process water that is made from surface water using residual heat by means of membrane distillation costs virtually no primary energy, and uses no chemicals. According to the RVO website, 125 PJ of residual industrial heat of above 100 °C is potentially available annually for this preparation process. With a residual heat consumption by the process of 200-500 MJ/m3, this will potentially lead to the production of 250-600 million m3 of process water per year. This is a significant amount, that can potentially be saved in energy and re-used in water using this technology. In addition to the energy saving potential, there are also quality advantages for the industry and possibly even cost savings because the heat in cooling towers no longer needs to be cooled as it can be re-used.