To achieve a fully circular economy we will have to be able to close our material but also our energy loops. Re-using, storing and upgrading energy is an essential part of creating a sustainable system. In the industry a large part of the energy usage comes in the form of heat. The FLEXSTEAM project, that kicked off on the 24th of January at TNO in Petten, aims to improve the way we can store and re-use thermal energy. Heat buffering is very important for the integration of heat pumps in existing industrial processes. By focussing on the efficiency of processes as well as replacing fossil resources with renewable ones we will be able to greatly reduce the industrial sectors’ dependence on fossil energy.
Upgrading and re-using industrial leftover heat
In the industry about a third of the energy is used to run processes that require temperatures under 250 degrees Celsius, often in the form of process-steam in the temperature range 150-250 °C. Left-over heat from these processes is now in many cases still cooled and drained away. Heat-pumps are able to upgrade fluctuating left-over heat. Upgraded heat can then be re-used in the designated industrial processes making the entire system more circular. The more efficiently this is done the more heat can be upgraded and less will go to waste.
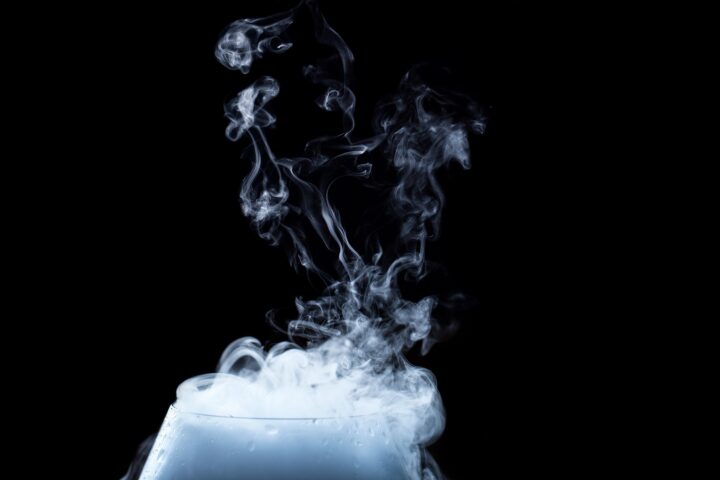
Phase Change Material, a thermal energy storage solution
A challenge lies in the storage of this energy when the availability of sustainable resources to run for example the heat-pumps varies. Storing energy is in fact one of the biggest challenges we face in the energy transition because of the varying availability of renewable resources. Electrical storage is very expensive whereas thermal storage can be achieved relatively cheap by using so called ‘Phase Changing Materials’ or PCM’s. Often a composition of salts or organic materials, PCM’s change from solid to liquid and in the process store latent heat. This way they can store a lot of heat in a small amount of volume.
Optimal industrial heat management
The FLEXSTEAM project falls completely in line with the TKI Energy & Industry’s program line for heat which states that its aims is: “to develop economically feasible technologies for an optimal industrial heat management with minimal residual heat by re-using process and residual heat using eg. heat pumps and by connecting supply and demand using energy storage”. This project aims to develop a cost-effective PCM heat-storage technology as a key-component for sustainable industrial energy-management.
Solar- and Geothermal energy to generate process heat
The technology developed will be used for the recovery and re-use of industrial leftover (waste) heat, directly as well as indirectly through the use of heat pumps. Apart from that it will also be able to increase the implementation rates of sustainable heat sources like geothermal and solar energy to generate process heat. Both can be used more effectively and efficiently if a thermal energy storage solution is present.
Starting the process towards industrial application
In the project three end-users will work together to develop a prototype where the heat-storage is based on PCM technology that is impregnated with heat-conducting materials in order to yield the necessary thermal output. The selected combination of PCM carrier material will be tested on a lab scale and a method will be developed for impregnation and production on an industrial scale. This will result in a PCM heat-storage concept that has been tested dynamically and will be ready to scale up for industrial application. This will be the basis for further development of a pilot scale project.
Acknowledgement
This project is co-funded with subsidy from the Topsector Energy by the Ministry of Economic Affairs and Climate Policy.